Photoluminescent Vinyl Sheets Rolls Wholesale Supplier Factory In China – KWVINYL
Photoluminescent Vinyl Sheets Roll is a self-luminous film through absorbs light then glows in the dark. It includes photoluminescent sheets, glow in the dark heat transfer film, glow in the dark fabric, and glow in the dark plastic material, etc.
KWVINYL is a glow in the dark sheet manufacturer, wholesale all kinds of glow in the dark materials, and accept OEM/ ODM order.
Our main products include Glow In The Dark Vinyl Sheet, Reflective Vinyl Sheets For Cricut, Glow in the Dark Heat Transfer Vinyl, Photoluminescent Rigid Sheet, Transparent Luminescent Film, Glow In The Dark Inkjet Photo Paper, and so on.
We also accept Custom Glow In The Dark Stickers with your design pattern. If you have any questions, please feel free to contact us.
Let’s get right to the main subject of this guide.
- 1. Photoluminescent Vinyl Luminous Principle
- 2. Photoluminescent Vinyl Manufacturing Process
- 3. Luminescent Materials And Applications
- 4. Photoluminescent Safety Signages Something You Need To Know
- 5. Photoluminescent Safety Signs 7 Major Advantages
- 6. Glow in the dark exit signs requirements
- 7. How to buy Photo Luminescent Tape
Photoluminescent Vinyl Luminous Principle
Photoluminescent Vinyl, a scientific name Glow In The Dark Film, can be luminous at night material. Through the absorption and release of visible light, let it shine in the dark night. Glow in the dark film can be used for a variety of safety signs, such as Emergency Exit Signs, fire safety signs, staircase signs, and so on.
Is Photoluminescent Vinyl harmful to the human body?
What is the working principle of glow film, harmful to the human body? It is a non-toxic, non-radioactive material, will not have any harm to the human body!
The structure of the photoluminescent vinyl film
Want to completely understand the material, the most direct way is to break it into each component. Glow In The Dark Film is composed of the mask layer, light storage layer, white glue layer, the adhesive layer, dependent protective layer.
- Mask layer is the role of protection of light storage layer, and can be in the above lettering, engraved patterns;
- The light storage layer is the core layer of the luminous film. It is composed of phosphor and glue fusion, the role is to store light and released light;
- White glue layer, also known as the reflective layer. Reflect the light emitted by the light storage layer, so that the light storage film looked brighter;
- The adhesive layer can be used to affix the object you want to paste;
- The dependent protective layer is to protect the adhesive layer isn’t contaminated.
Glow In The Dark Vinyl Luminous Principle
In summary, the light storage layer is the core of luminous film luminescence, and the core of the luminescent layer is phosphor. Phosphor also called luminous powder, it is derived from rare earth elements. Rare-earth element luminescence principle, through the rare earth element atomic electron energy level transition, to achieve the absorption and release of light. In other words, when there is light, the energy level of low electron absorption can reach its energy level transition energy, jump to high energy orbit.
When the light disappears or is weakened to a certain level, to reach the high-level orbit electrons release energy, transition back to low-level orbit, so as to achieve a luminous phenomenon. This process is repeated and will not decay. In other words, the luminous film luminous principle is actually through the phosphor atomic electron energy level transition to achieve, this process doesn’t produce any toxins and radioactivity. Because it doesn’t rely on electricity, it’s far more reliable than the electronic safety signs, but also energy saving!
The Prospect of Glow In The Dark Film
Visionary people know that glow in the dark safety signs has become safe signs irreplaceable products. The application of luminescent materials will become more and more extensive.
Not only safety signs but also the use of luminous film in heat transfer printing, which can be used as reference Luminous Heat Transfer Vinyl Leading Fashion.
Luminous Film Factory – KWVINYL
KWVINYL is Luminous Film Factory, wholesale all kinds of glow in the dark sheets, and accept OEM/ ODM order.
We provide free Glow Film samples, would you like to know more? Now Contact Us!
Photoluminescent Vinyl Manufacturing Process
The photoluminescent vinyl is made of an aluminate system, silicate system, and sulfide/sulfur oxide system. It can also be called luminous vinyl, glow in the dark tape, and photoluminescent tape.
In the natural light, fluorescent lamps, incandescent lamps, and other light sources after a certain period of time, can continue to shine overnight, people have been accustomed to calling it luminous film.
According to their application, they can be divided into two categories: organic light-emitting products made of organic materials and inorganic materials combined with inorganic products.
The main application environment of light-emitting materials is organic light-emitting products. With the expansion of applications, the varieties of luminous products are increasing.
In the preparation of organic light-emitting products, a lot of technical difficulties should be solved, such as:
- The contradiction between the refinement of luminescent materials and the decrease of luminescence properties
- Dispersion and poor settlement of luminescent materials due to the inconsistent density or particle size of the products
- Weatherability of organic light-emitting products used outdoors
- Problems in the production of luminous products, such as uneven contraction of the light-emitting plate and uneven luminescence.
Photoluminescent Film Structure
The luminescent film is a kind of functional film with a multilayer structure with light storage and luminescent material.
It is usually composed of a transparent protective layer, a luminous layer, a reflective layer, a pressure-sensitive adhesive layer, and a removable release paper layer, as shown in Fig. 1.
Each layer has different components and functions, and details are described below.

Fig. 1 Luminescent tape structure
Composition of each layer of photoluminescent tape
The ordinary photoluminescent tape is composed of five parts: transparent protective layer, luminous layer, reflecting layer, self-adhesive layer, and release paper layer.
The transparent protective layer is a transparent film made of organic resin, which can protect the luminous layer and improve the luster of the luminous film.
Photoluminescent layer
The luminescent layer is made of light storing luminescent material, carrier resin, plasticizer, auxiliary agent, and solution.
The thickness of the layer depends on the use, and the brightness of the luminous film increases with the increase of the thickness of the luminous layer.
When the luminous layer reaches a certain thickness, the brightness of the luminous film is no longer increased.
The thickness of the luminescent layer is usually in the range of 0.02 ~ 2.0mm, and the mass percentage of the material is:
Carrier resin 20% ~ 95%
Light storing luminescent materials 5% ~ 80%
Plasticizer 0 ~ 60%
Additives 0 ~ 30%
In a word, the brightness of the light-emitting film varies with the type of the luminescent material, the content of the luminescent material, and the thickness of the luminous layer.
Reflective Coating
Because the luminescence of the luminous layer spreads to both sides, the reflecting layer is added on one side of the luminous layer, and the luminous reflection of one side is emitted together with the luminescence of the other side so that the brightness of the luminous layer can be doubled.
The reflective layer can be a white or light-colored film or paper, also can be light or white paint coating, the white effect is best. The thickness can be controlled from 0.01 to 0.5mm.
The coating is coated with carrier resin, plasticizer, additive, pigment, and filler, and the mass percentage of each component is as follows:
- Carrier resin 10% ~ 98%
- Plasticizer 0 ~ 60%
- Additives 0 ~ 30%
- Pigment 2% ~ 80%
- Packing 0 ~ 40%
The adhesive layer usually selects acrylic resin or rubber resin, so that the luminous film has a self-adhesive function.
The release paper is a universal coated paper, which acts as an insulating adhesive.
Method for preparing the luminescent tape
There are many methods for the preparation of luminescent films. The basic principle is to disperse light-emitting materials uniformly in organic medium and form thin films. There are usually three basic methods for industrial production.
Blow molding
The flow chart of the luminous film prepared by the blow molding method is shown as follows.
The process is as follows:
- ① According to the design of the formula, weighing a variety of materials into the mixer, mixing materials evenly;
- ② The mixed material is made into luminous plastic granule;
- ③ The luminous plastic particles are sent into the extruder of the blow molding unit, heated and extruded, blown and cooled to form, and then the tube can be rolled up to obtain a cylindrical luminous film;
- ④ The tubular luminous film is cut open or printed with a white reflecting layer to obtain the luminous film;
- ⑤ The transfer coating process is used to prepare the pressure-sensitive adhesive for the luminous film, and the finished product is cut and packaged.
Advantages and disadvantages of luminescent films prepared by blow molding
Advantages are mainly reflected in:
- Compact equipment and low investment;
- Width and thickness of easy control film;
- The edge effect of the film without extrusion has high yield and low cost;
- The intensity of the luminous film is high.
The disadvantages are shown as follows:
- The cooling rate is too small and the film is poor in transparency.
- The film thickness deviation is larger.
- Mixing machine, extruder for material cutting larger, etc.
Calendar Method
Calendering is the main method for the production of plastic film and sheet, it is already close to the viscous flow temperature of plasticized thermoplastic plastics through a series of counter-rotating roller gap levels, so that the material under compression and extension, into a certain thickness, width and surface finish of the plastic film products.
Most of the plastics used for calendering are thermoplastic amorphous plastics, most of which are PVC.
Advantages and disadvantages of luminescent tape prepared by the calendering method
Advantages are:
- It has a large production capacity, high speed, and continuous production
- Product quality is good
- Flexible polyvinyl chloride film with a thickness of 0.05 ~ 0.5nm and a hard polyvinyl chloride sheet with a thickness of 0.25 ~ 0.7nm
- Comparison of the blow molding process
Disadvantages are:
- Huge equipment
- Higher investment
- Maintenance complexity
- In the production process, the light-emitting film will be subjected to repeated extrusion and shearing, and its performance will be affected.
Spread Plate
The coating method is to uses luminous material and organic resin to make luminous paint.
Using coating technology, the prepared luminous resin coatings are coated on different substrates.
The coating is made of gel, plasticizing, or drying process to make a luminous film.
The process flow chart of the preparation of luminescent film by a coating method is shown in fig. 4.
The luminescent film prepared by coating method has the following advantages:
- The linkage production line can be used;
- The production process is stable and the quality is easy to control;
- The production efficiency is high, the production speed of the linkage production line is 3 ~ 50m/min, up to 100m/min;
- It can be suitable for the production of various products. Such as film products, artificial leather, flooring, and so on.
The main drawback is the relatively large equipment, auxiliary equipment more.
Other Methods
The luminescent tape is produced in large quantities by the industrialized production method, which needs a larger investment.
A small amount of luminescent tape can be made by a screen printing method.
Specific methods are as follows:
- ① Light-emitting material and transparent ink (ink blending oil) are blended into luminous ink;
- ② Making screen with 80~150 purpose polyester monofilament mesh;
- ③ Choose white, light, or transparent substrates.
Using luminescent ink on the choice of good substrate printing, to ensure that the luminous coating meets the design requirements of the thickness. If the selected substrate is transparent, a white coating is printed after the luminescent layer has been printed.
Comparison of properties of various luminescent films
The luminescent tape made of ZnS: Cu and Co light storing material in aluminate system, silicate system, and sulfide system have the low luminous intensity and short afterglow time, which is difficult to meet the requirement of luminous throughout the night.
For example, in German standard 67510-4, the main technical indicators of luminous properties of the luminescent film made by ZnS: Cu, Co are shown in table -1. The light resistance and weather resistance of the light-emitting film is poor.
The light storage material adopts ZnS and aluminate complex, and the luminescent film is not ideal.
KWVINYL, such as PLO, SB, and REO, was used to produce blue, green, red, and other color luminescent films. The films had high afterglow brightness, long afterglow time, good light resistance, and good weatherability.
The luminescent properties of blue, green, and red light-emitting films produced by KWVINYL are compared with those of the previous ZnS-based luminescent films by table -2.
Application of luminescent tape
The new light storage luminescent materials have a wide range of applications: building decoration, transportation, military facilities, fire safety, daily life products, and other fields.
Especially, it plays an important role in the field of fire safety related to people’s life and property safety.
Sep. 2002, the American “Newsweek” in the “9·11” event of the first anniversary of the 《Five Who Survived》, reported the World Trade Center South Tower survivors to escape insider.
Among them, there is a description of the use of the light-emitting material produced by the luminous belt in smoke smell choking nose and dark corridor indicating the escape of people in the building. Excerpts are as follows:
Application of luminescent film in safety signs
Installation of luminous self-luminous evacuation sign system in buildings.
In June 1994, Germany developed a national standard for light storing self-luminous products (DIN67510-3) for evacuation. The standard specifies the performance requirements and setting requirements of luminous self-luminous evacuation sign system products. The standard has been adopted by European countries.
The United States is used Underwriters Laboratories UL 1994 standard, California Building Code (California Building Code) by the mandatory standard. This standard is adopted in most of the United States and some provinces in Canada.
Japan adopted the JIS Z 9100 (luminous safety signs board) standard formulated on February 1, 1987, which stipulated the performance requirements of refuge and escape sign products.
In April 2001 Chinese, People’s Republic of China Bureau of the Ministry of public security fire “building fire protection design standard”, “fire protection design of tall buildings” and “code for fire protection design of civil air defense works” by local provisions, mandatory requirements set light evacuation signs.
Photoluminescent Safety Signs Seven Major Advantages light a long time, low energy consumption, simple installation, long life, Easy to maintain, environmental protection, high reliability.
What do you need to pay attention to buying a luminous film? refer to How to buy Photoluminescent Tape
KWVINYL personalized customization service
KWVINYL is a customizable manufacturer of luminescent materials, We offer ODM/OEM products.
Contact us for free luminescent tape samples immediately.
Luminescent Materials And Applications
The luminous process of luminescent materials is the process of converting absorbed energy into light radiation. It is another kind of radiation besides thermal radiation, and the duration of this radiation is greater than that of light.
The production process of luminescent materials can be referred to as the Photoluminescent Vinyl Manufacturing Process.
The definition of luminescence
This definition of luminescence consists of two parts:
(1) Light-emitting from burning objects (such as incandescent light, solar light, etc.), without heat;
(2) The luminescence is different from the reflection and scattering of light, and the reflection and scattering of light have no lasting time, and the luminescence still lasts for a period of time after the excitation is stopped.
Classification of luminescent materials
It is necessary to ascertain whether the material is emitting without obvious boundaries. Under general excitation conditions, the material that does not luminescence also has weak luminescence under very strong energy excitation.
Some materials need to improve purity, luminescence can be stronger, and some materials need to be added to a certain amount of activator to have a stronger luminescence.
Materials that can glow under various forms of energy are called luminescent materials (or phosphors).
According to the different modes of excitation energy, the classification of the luminescent materials is the photoluminescence materials which are luminescent by ultraviolet light, visible light and infrared light. Photoluminescence materials are divided into long afterglow luminescent materials, light-emitting materials, and multiphoton luminescent materials, according to their different luminescent properties and application range.
A cathode ray luminescent material excited by an electron beam;
An electroluminescent material that is excited by an electric field;
A chemiluminescent material that causes luminescence by a chemical reaction between two or more than two chemical substances;
X-ray luminescent materials irradiated by X rays;
A radioluminescence material that is irradiated by natural or artificial radioactive materials.
Considerations for the purchase of reflective materials for reference: How to buy Photo Luminescent Tape
The concept of luminescence of luminescent materials
Some cathodoluminescence phosphors, such as radar phosphors, also have long afterglow after cathode ray ceasing. These materials contain sulfides and some fluoride. The afterglow time is longer than 1s, even up to 30s.
Luminescent phenomena and luminescent materials have played an important role in the national economy and people’s lives.
Long afterglow luminescent material is a kind of luminescent material that absorbs the exciting light energy and stores it and stops after light excitation, then releases the stored energy in the form of light, and it can last several or even more than ten hours.
The process of absorption, photoluminescence, storage, reemission, and infinite repetition is similar to that of battery charging, discharging, recharging, and discharging. Therefore, we suggest that long afterglow luminescent materials should be called light storage luminescent materials.
A brief history of luminescent materials
The earliest records of the luminescent materials in the West were in the jewels inlaid on the goods operated by the Italy Poloni shoe store.
The gemstone is made by calcining of ore and carbon, and it can be glowing in the dark. It was very precious at that time.
In 1603, the Italian man, Casciarolus, got some red minerals in the dark when he roasted the gold in the local ore.
Then by the analysis of barium sulfate containing components of stone, reduction roasting may become a part of barium sulfide, which is in fact after artificial preparation of barium sulfide storing type luminous material.
In 1609, Brand discovered the substance that gives white light to the air. It named it “phosphors”. Since then, the inorganic luminescent pigment is called the phosphor, sometimes it is also called luminophore.
There are two kinds of luminescence: phosphorescence and fluorescence.
Phosphorescence is derived from phosphor. It refers to the phenomenon of the long duration of light after excitation and stops. The light from long afterglow material is a typical phosphorescence.
The term refers to the fluorescence decay time is relatively short, generally refers to the phenomenon of less than 10-8s.
At present, people generally do not strictly distinguish between fluorescence and phosphorescence, which is called fluorescence when the time of afterglow is short to the indistinguishable by the human eye. The weak luminescence of afterglow is sometimes called the phosphor, and the light-emitting materials, which have a short afterglow time, are sometimes called phosphors.
From 1600 to 1700, many people, including Goethe, studied the luminescence of noctilucent materials.
Since 1764, the British people with oysters and burn out of blue luminescent material mixed sulfur, which should be the calcium sulfide luminescent materials.
It can be said that the discovery of the luminescent phenomenon begins with the light-emitting material. Many natural ores themselves are light-emitting materials, and people have already begun to use this kind of material to make various products.
Therefore, the light-emitting materials are the first kind of luminescent materials to be found and applied.
A systematic and scientific study of inorganic phosphors began in the nineteenth century. In 1852, Stokes and Becquerel, Verneuil and Lenard defined the first fluorescence definition and published the famous Stokes law.
At Sidoti in 1866, the luminescence of ZnS was discovered, and since then, ZnS has become the basis of many important industrial phosphors.
On the basis of the study of uranyl salt in 1867, two kinds of afterglow mechanisms were deduced, that is, Hyperbolic Attenuation and exponential decay.
In 1887, Verneuil realized that heavy metal impurities played an important role in the luminescence of inorganic substances.
In 1898, Mr. and Mrs. Curie extracted radium from uranium and radium bitumen, and radioluminescence materials began to be applied in all aspects.
In 1903 and 1904, Lenard and Klatt reported the relationship between activator and luminescence, first using flux and discussing its effect.
Urbach (1926), Randall, and Wilken deduce the different trap depths based on the different time constants of the afterglow attenuation.
The formal production and application of light storage luminescent materials began in the early twentieth century. The need for military and air defense in the Second World Wars also promoted the research and application development of these materials, but all these materials were sulfide series.
Before the 1970s, there had been no reports of non-sulfide light storage materials.
After that, though there were some brief descriptions about the long afterglow properties of the aluminate system, it was not until the 1990s that the aluminate system luminescent material with better optical storage property than sulfide was launched.
As soon as this new material is published, its excellent light storage performance has been recognized by people and is known as the second generation of light-emitting materials.
Luminescence principle of photoluminescent materials
In the crystal lattice formed during the synthesis of luminescent materials, structural defects and impurity defects have the properties of luminescence. Structural defects are the formation of vacancies and ions between the lattice points, also known as lattice defects. The luminescence caused by the lattice defect of the material is called self-activated luminescence.
In the process of high-temperature synthesis, the ions added into the matrix lattice formed the impurity defects in the high-temperature synthesis process. The luminescence caused by this defect is called activated luminescence. The elements to be added are called activators, and also called luminescent centers. Most of the luminescent materials that have been used in practical applications are mostly activated from luminescent materials.
For photoluminescence materials, the ultraviolet energy of the exciting material can be absorbed by the matrix (also called intrinsic absorption).
The matrix absorbs energy, and its luminescence can be directly generated by the recombination of valence band electrons and holes, and it can also be generated by the luminescent center formed by lattice defects or impurity defects.
This type of luminescent material is called a “composite” luminescent material. The sulfide series is representative of this kind of luminescent material. They are semiconductors, and the matrix lattice is the medium that produces the luminescence process. If the same activator is used to change the matrix component, the composition of the emission spectrum can be changed regularly in a wide range of wavelengths. When this kind of luminescent material is excited by ultraviolet light, the matrix absorbs energy first and then transfers energy to the luminescent center to produce luminescence.
Therefore, in the process of absorbing energy, transmitting energy, and emitting light, the composite luminescent material is lost and the efficiency of energy luminescence is low.
Ultraviolet energy can also be directly absorbed by the center of light when the material is excited. After absorbing the energy, the electrons in the center of the luminescence go to the high energy state from the low energy state. When the electron returns from the high energy state to the low energy state, it generates light. The materials that luminescent only relate to the electron transition of the luminescent center are called “characteristic” luminescent materials. The luminescent materials, such as silicate, phosphate, and aluminates, are characteristic luminescent materials based on oxygen-containing compounds.
The elements which are used as activators to form the center of luminescence are mainly transition elements, rare earth elements, and mercury-like elements. The luminescence process of the 5 materials is simpler than that of the composite material. The luminescence center directly absorbs the excitation energy, and the concentration is only a few percent. The energy between the center and the substrate is low so that the material has high luminous efficiency.
A schematic diagram of the luminescence process, as shown in Figure 2:
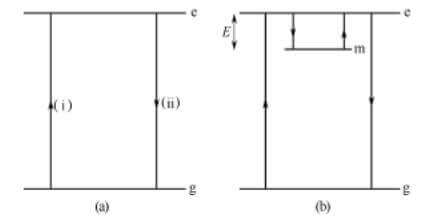
Figure 2 – energy level transitions in the production of fluorescence (a) and phosphorescence (b)
Electronic excited by external energy from the ground, “g” excited state “e”, namely, figure 2 (a) transition process (I).
When the excited electrons return to the ground state by photon emission, i.e. Figure 2 (a) in the process of transition (II).
The fluorescence transition (I) and (II) is the time interval between less than 10-8s, and this process is independent of temperature.
If in the excited state of “e” and “g” between the ground state energy gap “exists in the” metastable “level” m “[see Figure 2 (b)], the energy level diagram structure has changed from” g “, the electronic excitation to the” e “may be bound in the metastable state of” m “so, until the” m “from” e “to return to gain enough energy to reach E level,” e “will be able to return to the normal electronic transitions of G”, accompanied by light emission.
In this way, the delay time of the phosphorescence is in fact corresponds to the time that the electron stays in the trap “m”.
In fact, the basic storage and luminescence principle of light storing luminescent materials is similar to the schematic diagram in Figure 2 (b). In the light storing luminescent materials, the metastable m corresponds to the trap energy level, and the energy E corresponds to the trap depth.
The light storage properties of the sulfide series and the aluminate system luminescent materials are related to the trap energy levels of different depths in these materials.
When ultraviolet light is excited, trap energy with a certain depth of energy has captured a sufficient number of electrons from the excited state and stored.
After stopping the excitation of ultraviolet light, the electrons stored at the trap level gradually release 6 electrons at room temperature, and the electrons released are then transferred to the excited state, and the electrons grow back to the ground state from the excited state to produce afterglow.
Luminous principle of Luminescent Materials, reference Photoluminescent Vinyl Luminous Principle
The invention of nonradioactive material
There is an urgent expectation that materials that can glow for a long time and do not contain radioactive materials will come out as soon as possible. This expectation cannot be achieved by the series of sulfide light storage materials.
The afterglow time after the 1990s developed the aluminate light storage material has reached 2000min, the night light for a long time, the actual effect luminous digital symbol has more than permanent luminescent materials, the development of light storing materials entered a new era.
Europe was the leader of phosphor technology and industry before World War II. After the Second World War, the United States surpassed Europe, and after the 1980s, Japan began to gain an advantage in this industry. China has been catching up with Japan in recent years and has made great progress in some aspects. It occupies the world’s advanced level in the research and industrialization of new light storing luminescent materials.
The application fields of new light storage luminescent materials are very extensive. They are widely applied in the fields of building decoration, transportation, military facilities, fire safety, daily life products, and so on, and form the luminous industry chain. The market prospect is broad at home and abroad. Especially in the field of fire safety which is related to the safety of the people’s life and property, it plays an important role.
In September 2002, the American “Newsweek” in the “9 – 11” 1st anniversary with the theme of “Five Who Survived”, reported the survivors to escape insider, which is making use of the Glow In The Dark Stairs with the nose and dark corridor in the building after the evacuation instructions in smoke.
The luminescent material is applied not only to the safety mark but also to the thermal transfer printing, which can be used as a reference to the Luminous Heat Transfer Vinyl.
Photoluminescent Safety Signages Something You Need To Know
Photoluminescent Safety Signages include: emergency exit signs, fire safety signs, mandatory signs, warning signs, prohibited signs; in many emergency times, can save a lot of people’s lives.
As the Photoluminescent Safety Signages through the absorption of visible light, so as to achieve the effect of luminous. But also has non-toxic, non-radioactive, energy-saving and environmental protection, and other characteristics, so the scope of application is more and more widely.
For more luminous safety signs advantages, please refer to Photoluminescent Safety Signs 7 Major Advantages
All employers must ensure that the lives of employees and customers are safe, have the responsibility to tell them all the dangers in the work area, how to avoid the danger occurred in their own, and what happens after the danger to eliminate the danger; so in all office areas, factories and other places Must have a safety sign; the greater the area, the more necessary;
Assuming a large store fire, this time if there are no escape channel signs, familiar with the staff of the site maybe because of panic can not find the export, not to mention some unfamiliar customers, this will be the disaster ah! So the safety signs are essential.
Use of Photoluminescent safety signages
Application Of Emergency Exit Signs
Emergency Exit Signs: generally placed at a certain distance from the ground on the wall, or the floor of the landmark, there are some will hang up to indicate the location of the exit, closer to the ground is necessary because of the fire, often Smoke, because the fire smoke temperature is higher, the density is smaller than the air, are floating up, so the smoke at high, will affect the visibility of signs.
Application Of Fire Safety Signs
Fire Safety Signs: placed in the vicinity of fire equipment, such as fire hydrants, so that when the flames are found, to find fire extinguishers in a timely manner, put out small flames in time to avoid the fire spreading to the point where there is no control.
Application Of Mandatory Signs
Mandatory Signs: These signs are to tell people who enter a region, must be prepared to enter before, of course, each employer must let employees know in advance, this sign is reaffirmed, emphasizing the role! The most common requirements are helmets, safety shoes, goggles, and gloves.
Application Of Warning Signs
Warning Signs: This sign is to tell us what potential danger here, individuals should take self-protection behavior, ignore these dangers is stupid behavior; such as “high-risk danger” signs, if you ignore, may be fatal!
Application Of Prohibited Signs
Prohibited Signs: This sign is to tell us that those acts are not allowed, such as gas stations “forbidden fireworks,” private areas “forbidden to enter,” or some dangerous work areas need specialized training to get people, “non-technical staff, Prohibited to enter.”
These signs are very important, regardless of the day, or at night, have to make people clearly see; storage film safety logo, just absorb visible light, you can light in the dark 2-10Hr, during the day and night can be achieved eye-catching The role of the prompt.
Cherish life, safety will not allow the slightest sloppy.
Most countries have forced the use of Glow In The Dark Safety Signs in public places.
KWVINYL offers a variety of safety signs, including Glow In The Dark Vinyl, Photoluminescent Stickers, Glow In The Dark Printable Vinyl, Self Luminous Safety Exit, Glow In The Dark Fire Safety Signs, etc., according to the standard, you can also accept custom!
We offer free samples of Photoluminescent Safety Signage, would you like to know more? Now, contact us!
Photoluminescent Safety Signs 7 Major Advantages
Photoluminescent Safety Signs also are known as Glow In The Dark Safety Signs, the photoluminescent film luminous principle is actually through the atomic electron energy level transition to achieve, non-toxic, non-radioactive, energy-saving, and environmental protection, is the future development trend of Safety Signs;
How does photoluminescent signage work?
Photoluminescent signage operates by the principle of photoluminescent, occurring when an object absorbs photons from its surrounding environment and reemits them, creating a glowing effect. In nature, photoluminescence is usually a brief process, but the luminescent material used in egress markings and safety signage burns for up to ninety-six hours in total darkness.
Could photoluminescent signage work in a consistently dark environment?
If an environment remains dark indefinitely, photoluminescent signage will not work as intended. The solution to this problem is placing a black light in close proximity to the signage. Some building owners take this step to benefit from the superior dependability of luminous signage during emergency events.
If a building has backup lighting, why does it need photoluminescent signage?
Compared to photoluminescent egress solutions, backup lighting has disadvantages: it could malfunction due to generator failure or broken parts, and it performs poorly in the presence of smoke. Luminescent products, on the other hand, are electricity-free, contain no breakable parts, and remain remarkably visible in the presence of dense smoke.
What type of photoluminescent signage does my building need?
The type of signage a building needs depends on its construction and interior environment. Four signs that most commercial buildings need are floor identification signs mounted in vertical exit enclosures; emergency exit symbols mounted on all exit-leading doors; direction arrows indicating the direction of an egress path when its continuation is unclear; and “no exit” signs placed on doors that could reasonably be mistaken for exit-leading doors.
More and more people use KWVINYL Photoluminescent Safety Signs! The safe export indicator light is through the power of light, the whole working principle is controlled by a complex circuit chip.
The following is the circuit diagram of the safety exit indicator:
Comparison of LED Exit Sign Light and Glow In The Dark Exit Signs of the seven major differences:
Glow In The Dark Exit Signs | LED Exit Sign Light | |
Luminous duration | 2H-10H (after light) | 1.5H (after power failure) |
Energy consumption | Visible light | Power |
Installation | Paste, no professionals | Need professional guidance installation |
Service life | Indoor more than 10 years | Over 3 years |
Maintenance | No need | Professionals regularly check for maintenance |
Environmental protection | Non-toxic, non-radioactive | Nickel-cadmium batteries waste pollution of the environment |
Reliability | High, without any impact | Low, affected by the circuit |
Photoluminescent safety signs advantage
In summary, we obviously see: light long time, low energy consumption, simple installation, long life, Easy to maintain, environmental protection, high reliability is the advantage of the Glow In The Dark Exit Signs;
Like the fire, the elevator is not as safe as the stairs, the same emergency exit indicator light as the luminous safe exit is reliable;
Well-known, electrical equipment in the event of a disaster, very easy to damage, our Safety Exit Signs are for the accident when we can escape, it is not allowed to occur if the Safety Exit Signs can not be used.
Disaster may come at any time. Such as: In 1993, following a cruise ship fire that killed 158 people; In 2003, The World Trade Center was attacked on 9/11.
If we are unfortunate to meet the fire, even more, unfortunately, this time the emergency exit indicator light due to battery failure can not indicate the intersection, it would be how unfortunate thing;
The most unfortunate is that the lights have been checked out in advance, but because of the need for professional maintenance, but not timely maintenance, resulting in a disaster, can not find the export, I think this is what we do not want to see.
Photoluminescent Emergency Exit Signs, just absorb visible light, can light in the dark 2-10Hr, indoor life of up to 10 years, easy to change, paste it, you can quickly find the escape channel sign within 10 years. Cherishes life, safety will not allow the slightest mistake.
KWVINYL Service
Safety awareness of strong people has been in the use of KWVINYL Photoluminescent Safety Signs.
KWVINYL offers a variety of safety signs, including Photoluminescent Vinyl Film, Glow In The Dark Tape, Glow In The Dark Vinyl, safety exit signs, Photoluminescent Fire Signs, etc. According to the standard, also accept custom!
We offer free samples, would you like to know more, now contact us!
Glow in the dark exit signs requirements
Glow in the dark exit signs requirements: everyone in the workplace must know the relevant fire safety information so that in case of fire or other disasters, employees can escape in time. In terms of fire safety signs, this means that everyone must know the location of the fire alarm and emergency equipment, understand the location of the fire channel, and how to enter safely.
In the past, it has been proved that export signs can save a life. In the event of a fire, keep a calm mind, and find the nearest emergency exit to ensure the greatest chance of escape. It is easier to complete with the help of the exit sign. Safety export marking is very useful and is considered mandatory in any facility. More importantly, there are strict regulations on what exit signs are required. In most cases, the glow in the dark exit signs is cheap, effective, and fully consistent with all safety specifications and regulations.
Photoluminescent Safety Signs Seven Major Advantages light long time, low energy consumption, simple installation, long life, easy to maintain, environmental protection, high reliability.
The individual requirements for fire safety signs in your workplace will be decided by a personal risk assessment of your business. However, the following concise guidelines for fire safety signs introduce the main safety signs and indicate which circumstances you should use.
What is a fire safety sign?
Fire safety signs are used to provide health and safety information to warn of danger, to provide instructions, or to provide you with safety information. Security signs can be a variety of colors – usually red, green, yellow, or blue, and may contain images, words, or a mixture of both. It is very important to observe the fire safety signs in the workplace and any other public places: they are at your side for your safety, and neglect will have serious consequences.
Why is the fire safety sign important?
In 2005, the management reform (fire safety) decree stipulates that all workplaces must have enough safety signs to instruct people to fire equipment, emergency routes, and emergency exits.
The American Occupational Safety and Health Administration (OSHA) defines the export route as a safe place from any location in the workplace to an emergency. This includes all exportation, export, export, or aisle, from export to a public passageway or other security areas.
This legal requirement is crucial, because there is no proper sign, and you may put your employee’s life in danger. According to the health and safety law, all employers have legal responsibilities to ensure their health and safety at work: fire safety signs are only one of the many things that can be done to comply with this requirement.
Glow in the dark exit signs design requirements:
Exit signs must have a clear and readable letter “EXIT”, which is at least 6 inches, and the stroke width (the width of the letter) is at least 3/4 inches. Signs and letters must be unique colors that provide high contrast between the letters and the background.
There are some temporary exit signs, usually just printed on a piece of paper. Because of the lack of visibility, these are unacceptable. In order to make the exit sign effective, it must be able to see the exit signs in emergency cases, such as a fire. Glow in the dark exit sign is the best solution, because it doesn’t need a power supply, and luminous exit signs can shine through the absorption of visible light when the light is insufficient. Please refer to the luminous principle of glow film: Photoluminescent Vinyl Luminous Principle
What is the regulation of glow in the dark fire safety signs?
The following “1996 health and safety (safety signs and signals)” Regulations on fire safety signs provide some guidance, indicating what signs should be used, and how and where to install them.
- Fire safety signs should always be clear and clear – ensure the use of fire safety signs to clearly and effectively indicate the escape route and to export in the event of a fire.
- The escape routes and doors must be marked clearly. Any door confusing with the emergency exit door should be marked with clear signs or notices, or signs or notifications as “no-export” or “no way out” or marked “storehouse”.
- The signs for escape routes must be displayed along the export routes, which should be changed in all directions of corridors, staircases, open spaces, and all doors or intersections.
- Fire safety signs should be lit – so that they can always be seen and clearly visible, including in the case of power loss.
- The direction arrow is included in the escape route sign to indicate the fastest way to safety. Wherever you are, you can see the nearest escape route sign immediately. Each flag contains the direction arrow, pointing to a more effective route.
- The final export fire signs should not have arrows – the emergency exit signs above the exit gate should not have arrows. Instead, they should be replaced by the image of a running person, or simply “quit” or “quit”.
- Don’t mix signs – stick to all European standard signs or all British standard signs: don’t mix the two.
- It is recommended that the fire safety instructions be supplemented with the form of pictures. The signs must be suitable for all users, including those with poor eyesight, who are suffering from dyslexia or no English as the first language. The supplementary text will also ensure that the meaning of the graphic symbol is fully understood. The disability discrimination act further stipulates that the disabled must make “reasonable adjustments”, including displaying braille and tactile fire safety signs beside the standard picture signs.
- The sign should be placed at the right height – the sign needs to be visible far away (the British Standard Association can find complete guidance in the BS 5499 fourth section). The sign on the door should be 2 meters away from the ground, or below 2 meters from the ceiling, and the mark on the wall should be 1.7 meters away from the ground.
- The enterprise should introduce the different fire extinguishers in the workplace to the employees – the diagrams of different types of fire extinguishers and information about the 6 categories of fire symbols.
- All employees should know the location of the nearest fire alarm and how to do it in case of an emergency. This is a legitimate requirement, and we can use trainers to use the “fire alarm point” sign and show the location of the fire operation notice.
- Fire equipment must mark signs – for example, a sign indicating the position of a fire hose reel or fire extinguisher.
Display of export signs:
The export signs of each person must be clearly marked. In addition, if the export route of a particular working area is not immediately apparent, a sign must be posted on the route to indicate the direction of the export.
If the exit or passageway of the export passageway cannot go to the exit, it may be mistaken for export. It must be clearly marked “not exported” or marked with the purpose of indicating the purpose of the area, which clearly indicates that this is not an export.
Exit signs must be placed in clearly visible areas, with clear lines from any working area. Any ornament, curtains, or other signs shall not be placed in a place where the visibility of the exit signs may be obstructed.
What fire safety marks are needed for firefighting equipment?
“2005 regulatory reform (fire safety) Order” thirteenth provisions: any non-automatic fire protection equipment is easy to use, the mark is clear. The signs used are as follows:
- Fire Extinguisher Sign: displayed next to all fire extinguishers to easily identify the location of the nearest extinguisher.
- Fire Alarm Call Point Sign: located at all fire alarms.
- Fire Hose Reel Sign: located at all fire hose points
- Fire Blanket Sign: located at all fire blanked locations
- In Case Of Fire. Do Not Use The Lift Sign: displayed at all lifts alongside the “Use Stairs” sign to indicate a safe escape route.
What fire safety marks are needed for emergency exportation?
“The 2005 regulatory reform (fire safety) Order” fourteenth provisions, “emergency routes and exports must be marked by signs.” The signs used are as follows:
- Fire Door Keep Shut Sign: displayed on each side of all fire doors to ensure safety.
- Fire Exit Sign: displayed along all designated fire escape routes (with arrows) and above all emergency exits (without arrows).
- Fire Assembly Point: a pictogram or written sign displayed at the outside point of assembly where people must gather after evacuation.
- In Case Of Fire. Use Stairs Sign: an information sign displayed next to lifts and the top of staircases so people know not to use the lift for safety reasons.
Firefighting signs start from the direction arrow, showing the safest and fastest emergency route. Please note that the last fire channel sign above the emergency exit door does not display the direction arrow.
How to buy Photo Luminescent Tape
Photo Luminescent Tape is more and more widely used by people all over the world.
The Photoluminescent Tape can be used as Safety Signs, but also very fashionable, so the Photo Luminescent Tape is used by many families and workplaces!
You can refer to Photoluminescent Safety Signs 7 Major Advantages.
The Photo Luminescent Tape absorbs visible light, and when the light is weakened, the visible light is released, through the storage of rare earth elements in the energy level transition to achieve the effect of light, non-toxic, non-radiation, safe, and environmentally friendly.
Can be used on the stairs, and some need to indicate the place, To prevent a sudden power outage, resulting in operational security risks.
Can also be made into a variety of small ornaments, placed in a child’s bedroom, luminous can bring children safe, accompany them to sleep peacefully.
Can also be used for various meetings, looks very cool, and so on.
There are seven main colors of the luminescent film on the market: Yellow-green, Khaki, Pink, Orange, White, Green, Blue, and the colors of night light are Green, Yellowish green, Orange, Orange, Blue, Green, Yellow-green.
How to judge Glow In The Dark Vinyl is good or bad?
In fact, is suitable for their own Glow In The Dark Vinyl, different price of the Photoluminescent Tape, the effect is naturally different.
Photoluminescent Film Nontoxic, non radioactive
There are a lot of people who will worry about the Photoluminescent Tape will have radiation.
In fact, as long as we understand the principle of radiation, we know how to determine whether the Photoluminescent Tape radiation.
Radiation is through the continuous attenuation of radioactive atoms, the release of energy, it seems the same effect of light if it is phosphor into the reflective atoms, is the radiation can be excited by the Photoluminescent Tape in the rare earth element electrons, which has been shining until the radioactive atoms Decay to the stage where the human eye can not be identified.
Knowing the principle of luminous, we can easily determine whether the Luminescent Tape contains radioactive material.
When the light on the Photoluminescent Tape disappears, the Luminous Tape generally can only maintain 2 ~ 12H, and the process is bleaker and bleaker, And radioactive material is not very easy to dim, as long as the Luminescent Tape can not be exposed to the place where the 24h (such as drawers), and then observe the light in the dark whether the Photoluminescent Tape.
If you can see the obvious light, the description is containing radioactive elements.
On the other hand, it shows that there are no radioactive elements in the Luminescent Tape.
Knowing more about the Luminescent tape can be used as a reference Luminescent Materials And Applications
Photo luminescent Tape luminescence time
The luminescence time of the luminescent film is determined by the rare earth elements in the luminescent film.
There is a long time, and the time is relatively short.
The general time is distributed in 2-4h, 4-6h, 6-8h, 8-10h, 10-12h.
This is in accordance with the individual need to buy, the general price is proportional to the time with the light.
The luminous brightness of the Photoluminescent Tape is determined by the amount of phosphor per unit area, the more the phosphor per unit area, the longer the light-emitting time, the more bright, the higher the price.
Photoluminescent Tape Surface Materials
The Photoluminescent Film surface is PET, PVC, PMMA different surface film, the price of PMMA higher than PVC, PVC higher than PET.
PMMA has good weather resistance, but because it is more brittle, easy to tear, the price is expensive, the application will be less.
PVC is based on the PET in the increase in a layer of PVC film, more than one material, another process, the price will be more expensive than PET.
PVC film made of Photoluminescent Film can be used for printing, printing, printing, photo, suitable for mass printing.
PET film can be used for engraving words, not suitable for large quantities.
When you purchase Photoluminescent Tape, it is recommended to make decisions based on market demand, not necessarily the price of the better, the right is the best.
KWVINYL offers a variety of safety signs, including Glow In The Dark Tape, Photoluminescent Film, Glow In The Dark Exit Signs, Fire Safety Signs, etc., according to the standard, you can also accept custom!