China Reflective Sheeting Manufacturing Factory Trading Company – KWVINYL
Are you still looking for retro reflective sheeting companies? Now you can stop searching. KWVINYL is Retro Reflective Sheeting Manufacturing Suppliers in China, wholesale many kinds of reflective materials, and accept OEM/ ODM orders.
Our reflective sheeting comes with an adhesive on one side with a paper backing that protects the adhesive until exposed. The Reflective vinyl has a permanent adhesive. It is compatible with all personal hobbies and craft cutters and can be used in many applications including car decals and signs. It can be used indoors but is waterproof and weather resistant making it an ideal craft vinyl choice for outdoor applications as well.
Reflective Sheeting Purchasing Guide
Reflective sheeting is one of the reflective products of KWVINYL, made of Acrylic/PC/PET/PVC or mixed face film, our reflective material customers can choose the right reflective film according to their products, PVC reflective vinyl is suitable for digital printing, the acrylic reflective sheets are suitable for screen printing, PET reflective sheeting can be adapted to plotter cutting, and all of them can be used for UV printing.
Of course, if you have strict requirements for reflective values, we also offer reflective films with different reflective values.
Our main products include Prismatic Reflective Sheeting, Reflective Sheeting Rolls, HIP Grade Reflective Sheeting, Engineer Grade Prismatic Reflective Sheeting, EGP Reflective Sheeting, Reflective Sheeting For Traffic Signs, High Intensity Grade Reflective Sheeting, and so on.
We also accept custom reflective stickers with your design. Now, contact us to know more details! (E-mail: [email protected])
Chapter 1: What Is Retro Reflective Sheeting
Retro Reflective Sheeting, also called reflective vinyl, retroreflective film, is a kind of retro-reflective material that has been made into a thin film for direct application. It is made using glass bead technology, micro-prism technology, synthetic resin technology, thin-film technology, and coating technology, and micro-replication technology. Typically available in white, yellow, red, green, blue, brown, orange, fluorescent yellow, fluorescent orange, fluorescent yellow-green, as well as fluorescent red and fluorescent pink.
Reflective vinyl is not self-luminous. It has no noticeable properties under normal daylight conditions. It is specifically designed to be seen at night when struck by artificial light, such as that from car headlights. This reflective property makes the road sign visible after dark without the need to spend electricity on illumination. As a result, the color shift sometimes occurs when reflective vinyl is viewed in different settings.
For example, a white reflective film is white only when it is operating. At normal daylight settings, it tends to look slightly gray or pearlescent. At the other end of the spectrum, a black reflector must look different when light hits it because black is the reason there is no light. As a result, the black reflector will look brown when reflecting light after dark.
Chapter 2: The History Of Retro Reflective Sheeting
In 1937, the world’s first retro reflective sheeting was born in a laboratory in the United States, which was the beginning of the history of large-scale application of reflective sheeting for traffic signs. In 1939, in the United States, Minnesota highway side, for the first time in the open-air conditions used a sign made of reflective film, from then on, unveiled a series of reflective products for traffic signs of the new period, creating a new traffic safety industry. That year, the use of reflective vinyl for traffic signs was officially mandated in the U.S. National Standard for Traffic Signs (Manual of United Traffic Control Devices, 1939).
Since then, with the development of the chemical industry, especially synthetic resin, various research and development institutions have continued to research and innovate, using glass bead technology, synthetic resin technology, film technology, and coating technology, developed a series of high-quality retro-reflective products one after another.
Starting from the 1940s, this first reflective film was named “engineering-grade” reflective film and began to be widely used for road traffic signs. Since then, a series of products such as reflective films for personal safety protection in the field of clothing were also developed along with the advent of synthetic resins to meet the needs of social development. Afterward, with the research results of a series of material science and technology and optical technology, especially the emergence of micro-prismatic reflective materials, this kind of reflective material, which was mainly used for traffic signs at the beginning, began to be gradually replaced by newer and better reflective materials.
Chapter 3: Types of Retroreflective Sheeting
Not all retroreflective sheeting is created equal. There are many ways to classify reflective sheeting. One of the more commonly accepted classification principles is based on the basic structure of the retro-reflective unit, and the ranking method is based on the higher or lower retro-reflectivity coefficient of the reflective sheet’s frontal luminous performance. However, considering the different processes of reflective sheets, some of which are specifically designed to address non-frontal retro-reflective luminance, some of which are designed to address both, and some of which are designed to address the visualization needs under harsh weather conditions, there are shortcomings in this classification method. Therefore, it is essential to be familiar with and understand the application conditions and design functions of the various types of reflective films. Traditionally, reflective sheeting are divided into two main categories, glass bead reflective vinyl and prismatic reflective sheeting, according to the structure of the reflective unit of the reflective sheeting. These are further segmented into different Types and grades determined by their construction and reflective properties, which we’ll examine in a moment.
3.1 Classification By Structure
3.1.1 Glass Bead Type Reflective Film
Glass bead reflective films are made by mixing glass beads in the mask’s pigments for retro-reflection. When illuminated, the embedded beads reflect the light back to the observer. For this reason, retro-reflective films are also known as glass bead reflective vinyl.
These embedded beads make retro-reflective sheets more difficult to cut than standard PVC vinyl. Always use a 60° blade when cutting retro-reflective foils. You can use a 45° blade and a lot of force to make it work, but the blade will be worthless when you are finished.
Glass bead type reflective films were introduced earlier, but with less process variation, there are two main types, lens-embedded reflective films, customarily known as engineering grade reflective films, and hermetically encapsulated, often referred to as high intensity reflective vinyl. In the lens-embedded reflective sheeting, due to its long history of emergence, different manufacturers, during the long production and manufacturing process, made use of the different diameters of the lens, density and thickness of the weather-resistant coating to produce many kinds of reflective sheeting, such as high intensity reflective sheeting, mainly on the basis of engineer grade reflective sheeting, with higher quality glass beads, and increase the density of glass beads to improve some brightness; commonly known as “commercial grade reflective vinyl”. The commercial-grade reflective sheeting, mainly produced in China, is basically based on the technology of engineering grade reflective vinyl, which is achieved by reducing the number and density of lenses (glass beads). These two types of reflective film, economic grade reflective film, whose reflective ability cannot meet the needs of traffic safety, are more often used in the commercial field, in accordance with the ASTM D4956 Type III standard.
3.1.2 Microprismatic Reflective Sheeting
Each type of reflective sheeting also contains many types, such as micro-prismatic type reflective sheeting, due to the use of more advanced technology process, its material selection, and prism structure, there are many changes, can cope with more traffic demand. According to the form and technical characteristics of the prism, the micro-prismatic reflective film can be divided into truncated-angle prismatic reflective vinyl with good retro-reflection ability at a long distance, truncated-angle prismatic reflective sheeting with a good retro-reflection performance at a short distance and large angle, full-prismatic reflective sheeting that takes into account various needs, fluorescent full-prismatic reflective vinyl with good performance in the daytime and under harsh weather conditions, prismatic retroreflective sheeting that conforms to traditional engineering-level retro-reflection parameters and so on.
Prismatic reflective vinyl is made by layering small prisms in the face film. Upon close inspection, they look like small pyramids in vinyl (Fig 1). Just as a prism splits and reflects light, a prismatic reflective film reflects light back to the viewer through the face film.
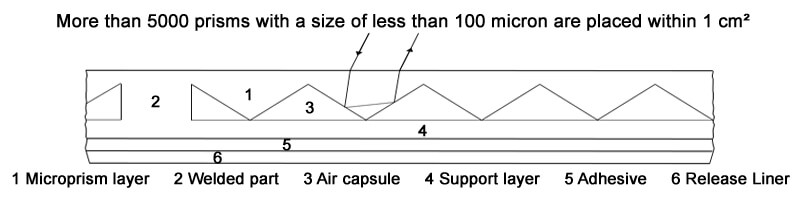
Prismatic reflective film is made by layering small prisms in the face film. Upon close inspection, these would look like tiny pyramids in the vinyl.
This dense, layered structure makes prismatic retro reflective vinyl more difficult to cut than retro-reflective films. Some brands, such as 3M 3930 Diamond Grade, can only be cut with Pro Series knives using a special blade and over 400 grams of force. If your 3M vinyl is wider than 24 inches, you may need to add a compression roller to the plotter. The cutting force used to cut the film may cause tracking problems. An additional compression roller helps to align the media properly.
Other brands, such as Nikkalite’s Crystal Grade reflective sheeting, can only be cut with a flatbed cutter. They can be scored using a Pro Series plotter, but the cut must be completed manually.
The advantage of prismatic sheeting is that the sides of the prismatic units in the mask reflect light at a wider angle. This results in more light being reflected back to the light source and makes that light visible from a wider angle of view. This is particularly useful in highway signs, which is why the prismatic sheet is the spec for this application.
3.2 Classification by adhesive
According to the backing type of reflective vinyl, reflective sheeting can be divided into heat transfer reflective vinyl, pressure-sensitive reflective sheeting and non-backed reflective vinyl. The traditional reflective films used in the field of traffic facilities are mainly pressure-sensitive. Pressure-sensitive backings adhere to smooth, clean surfaces without heat, solvents, or other preparations, and traffic signs are typically affixed to aluminum or aluminum alloy sheet surfaces. The adhesion of thermal adhesives is triggered only when the heat is applied to the material and pressure is applied. The reflective film without adhesive backing is commonly used for self-supporting materials manufactured from traffic cone reflective tape, temporary roll up warning signs, and facility post reflective tape.
3.3 Classification by national standards
Talking about the scientific classification method of retroreflective sheeting, we cannot leave the reflective sheeting standards that have great guidance on the application of retro-reflective sheeting. Among the reflective vinyl standards in the world, the American Society for Testing and Materials standards, Australian and New Zealand standards, Chinese reflective sheeting standards, the U.S. Federal Highway Administration traffic sign retroreflective material guidelines, etc., have played a positive role in guiding the research and application of retroreflective materials to make traffic signs and improve traffic safety in countries around the world. Below, we will introduce them one by one.
3.3.1 Classification by ASTM standards
The American Society for Testing and Materials is a long-established international organization for materials testing standards, known as the Association of Standard Testing of Materials (ASTM), which was established to provide the scientific and industrial communities with a series of materials testing standards to achieve the definition of new materials for We provide a technical platform for the worldwide scientific community to exchange ideas. Provide technical support for the standardization of testing of retro-reflective materials and many other materials used in various industries such as oil, gas, and chemical.
In view of this technical backtracking, ASTM’s test standards for retroreflective materials are cumulative with the invention and use of retroreflective materials, and each time a new material has been available for a period of time and its manufacturer has applied to ASTM for membership, its committees are authorized to define categories and establish test standards for that material. It is for this reason that the number of reflective sheeting types in ASTM D4956 is eleven and counting; however, on the other hand, the ASTM standard is more of a catalog of retroreflective materials than a standard that helps to understand the methods and problems of retroreflective sheeting applications, because in its original classification of these materials, ASTM did not consider Drivers’ performance and needs.
For this reason, in order to provide more effective technical support and guidance to their own traffic engineering construction units, developed countries around the world have set up their own national technical standards, rather than directly following the ASTM classification of reflective materials.
The following 1, 2 classifications are the recommended classifications of retro-reflective materials developed by FHWA on the basis of ASTM, which clearly distinguish between traffic signs and non-traffic signs by combining the structural characteristics of glass beads and prismatic retro-reflective materials.
1. US Federal Highway Administration Classification Method for Retroreflective Materials – September 2005 (Reflective Films for Traffic Signs)
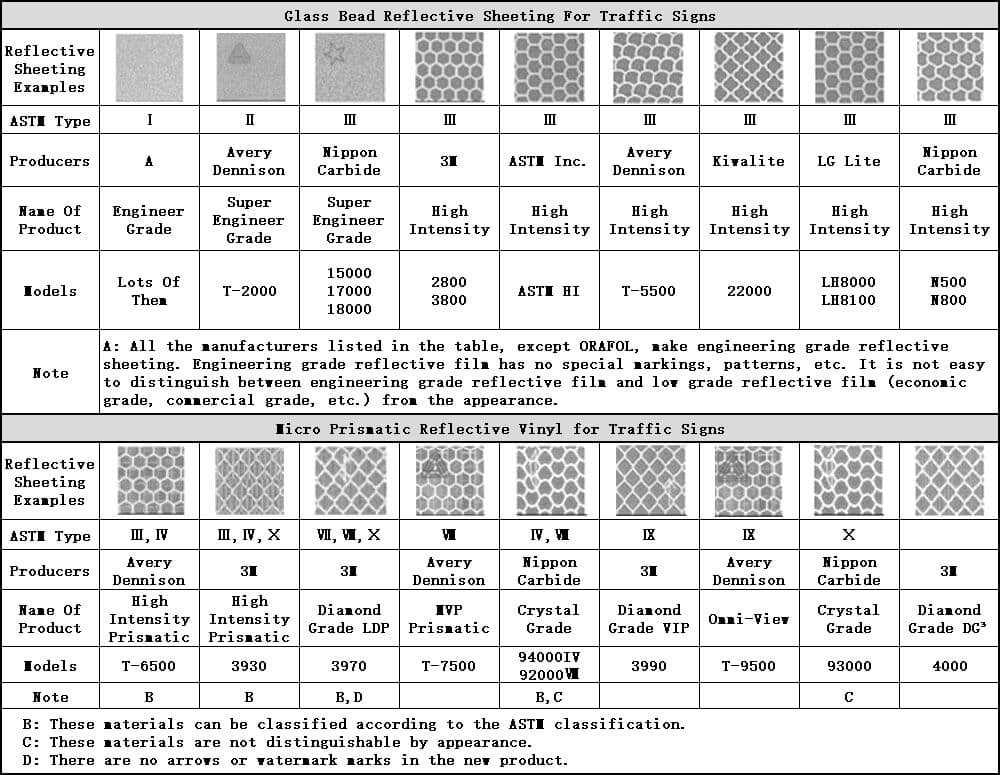
Table 1: FHWA’s Classification of Retroreflective Materials
2. FHWA Classification Methodology for Retroreflective Materials – September 2005 (Reflective Films for Traffic Cones, Traffic Bollards, etc.)
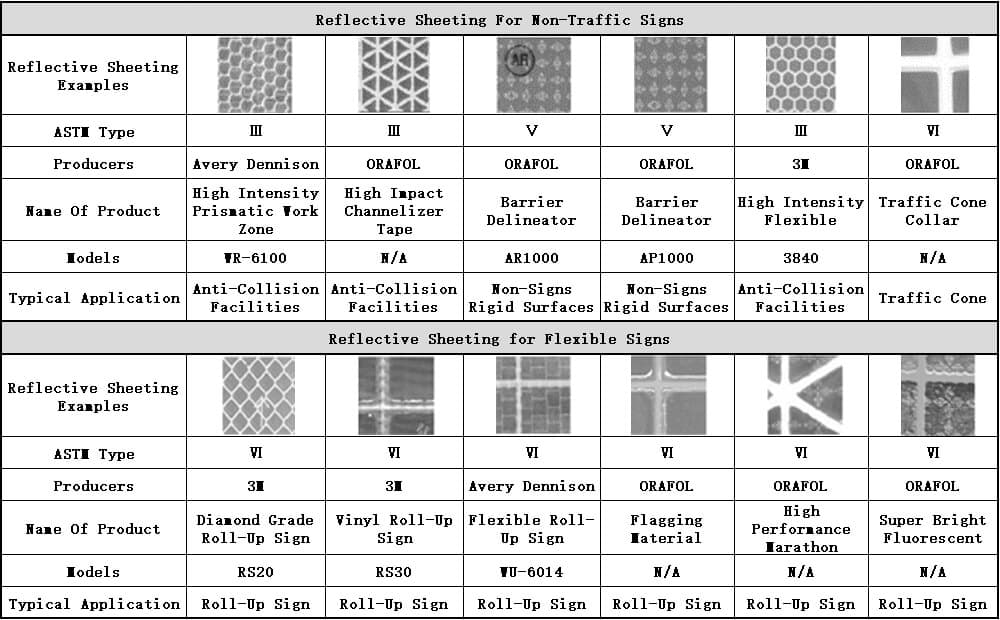
Table 2: FHWA’s Classification of Retroreflective Materials
Quantification and Standardization: ASTM D4956
There are reflectivity standards that allow the effect of different films to be graded. These standards form the basis for government regulations and codes that control reflective vinyl. Measure and measure the amount of light reflected by a reflective vinyl, expressed in cd/lux/m². In other words, it is the reflected light measured in candlelight at various viewing angles. This value can be viewed if you want to compare reflective vinyl based on visibility at different angles. For example, the KWVINYL Engineer Grade Prismatic white reflective vinyl has a rating of 185 at a viewing angle of 0.2°. By comparison, the ORALITE 5700 and ORALITE 5800 have ratings of 100 and are rated at 250 respectively. Of course, these are white. The colors will have lower ratings.
Technically, if you want to compare candlelight-based vinyl, you have to look at various viewing angles and various angles of incidence (remember, these are designed to simulate real-world conditions.) You rarely feel like you’re reading a road sign on a street sign. The dark night is right in front of you. (If it were, you would read it and then run into it). A complete chart of reflectivity can be found in the product data sheet for any reflective vinyl (Table 3).
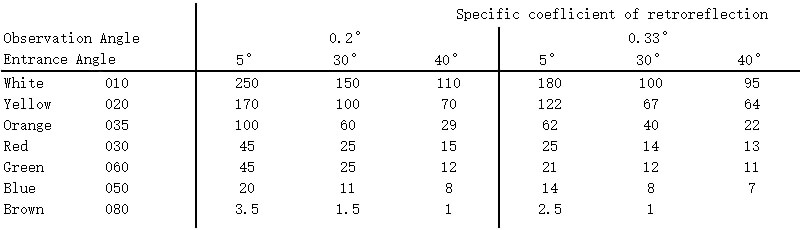
Table 3: You can pore over a complete chart of measured reflectivity, or just make sure the vinyl meets an industry-standard called ASTM D4956.
However, you don’t have to check the numbers, but simply check to ensure that the vinyl under consideration meets the industry standard known as ASTM D4956.
ASTM D4956
ASTM is an international standards organization originally known as the American Society for Testing and Materials. ASTM standards are used to evaluate thousands of products. The D4956 standard is the standard specification for traffic control retroreflective sheeting. Therefore, if the vinyl complies with the ASTM D4956 standard, the vinyl can be safely sold and installed for use in road signs. However, the D4956 standard references ten types that cover different applications and reflectivity levels. Type I, II, and III are different types of retro-reflective films. Type IV-X are prismatic structures.
3.3.2 Classification by Australian and New Zealand standards for retro-reflective materials for road traffic signs
The Australian and New Zealand standards for retro-reflective materials for road traffic signs provide more concise and clearer guidance than the guidance provided by the Federal Highway Administration in the United States. Many countries, including China, are influenced by this standard to varying degrees, particularly many European countries.
Table 4 Australian/New Zealand standard for retroreflective sheeting for traffic signs (AS/NZS1906.1:2007)
Grade | Structure | Performance | Applications |
---|---|---|---|
1W | Micro-prismatic Structure | Ultra-high equivalent reflective strength, especially at the large incidence and observation angles. Typically has a service life of 12-15 years. | Suitable for roadside and gantry signs, especially for text and directional information. |
1A | Micro-prismatic Structure | High reflective strength, especially at long distances and at small viewing angles. | Outline |
1 | Mostly hermetically encapsulated glass bead construction | High reflective strength typically has a 12-15 year lifespan | Suitable for side markings on motorways and urban roads. |
2 | Mostly lens-embedded glass bead construction | Medium reflective strength typically has a 7-year lifespan. | Suitable for roadside signs that are very close to the road surface, and where the surrounding environment is dark and identification from a distance is not required. |
2A | Mostly lens-embedded glass bead construction | Medium to high reflective strength typically has a 10-year lifespan. | Pretty much the same as 2, except that the guaranteed life is 10 years. |
1W (CW) | Micro-prismatic Structure | Same as 1W, but with better flexibility, no quality warranty | Construction zone facilities |
1 (CW) |
Mostly hermetically encapsulated glass bead construction | Same as 1W, but with better flexibility, no quality warranty | Construction zone facilities |
There are some highlights in this latest version of the 2007 Australian and New Zealand standards that are worth noting. The standard, which is based on nearly 15 years of research results from the international traffic safety engineering community, focuses on new safety requirements and reflects the latest trends in traffic sign retroreflective technology standards in a number of developed countries, including the UK, Sweden, the Netherlands, and Spain, including.
- 1. 1W (wide angularity) replaces the traditional 1A (frontal brightness only) position on traffic signs with 1W (wide angularity), which is converted to reflective film for contour markings.
- 2. The advantages of large-angle reflective films (class 1W) for traffic sign applications are extensively described in the preface, with emphasis on the importance of large viewing angle performance in sign reading by drivers.
- 3. Reflective brightness of a 1-degree viewing angle has been added to all levels of reflective film performance requirements.
- 4. The selection and use of reflective films are specifically described in appendix B to the standard.
1) Said that the selection of reflective film should be based on a variety of factors such as performance, weather resistance, and price, and clearly pointed out that choosing the product with better weather resistance is more economical in the long run.
2) Introduced the locations and roads where reflective films of different levels are applicable.
3) Introduces the changes in the viewing angle of a driver reading a sign, and points out that as the viewing angle increases, the brightness of the traffic sign should remain relatively stable, and that reflective film with a large difference in front and back brightness is not suitable for making traffic signs and also points out that the reflective brightness should remain stable even when driving different types of vehicles.
3.3.3 Classification according to China reflective sheeting standard
The Chinese standard for reflective sheeting is GB/T 18833-2012, Road Traffic Reflective Vinyl. According to its photometric structure and use, the reflective film is divided into seven types.
Type I Reflective Sheeting, usually lens-embedded glass bead structure, called engineering grade reflective sheeting, service life is generally 7 years, can be used for permanent traffic signs and work area facilities.
Type II Retroreflective Vinyl, typically a lens-embedded glass bead type structure, called super engineer reflective vinyl, with a typical service life of 10 years, can be used for durable traffic signs and deteriorated work zone facilities.
Type III Reflective Film, typically a hermetically sealed capsule glass bead type structure, known as High Intensity Grade reflective film, with a typical service life of 10 years, can be used for permanent traffic signs and work zone facilities.
Type IV Reflective Sheeting, usually of micro-prismatic construction, called super-intensity grade reflective sheeting, with a service life of typically 10 years, for use on permanent traffic signs, work zone facilities, and contour markings.
Type V Retro Reflective Sheeting, usually of micro-prismatic construction, called the large-angle reflective film, with a service life of 10 years, can be used for permanent traffic signs, work area facilities, and profile markers.
Type VI Retro Reflective Vinyl, usually of microprismatic construction with metallic coating, with a typical service life of 3 years, maybe used for outline signs and traffic bollards, or, without metallic coating, for work area facilities and traffic signs with few characters.
Type VII Retroreflective Sheeting, usually of microprismatic construction, flexible material, generally with a service life of 3 years, maybe used for temporary traffic signs and work area facilities.
Chapter 4: Structure of Reflective Sheeting
Reflective sheeting is composed of layers of different materials with different properties, and the layer structures of the different reflective membranes are different.
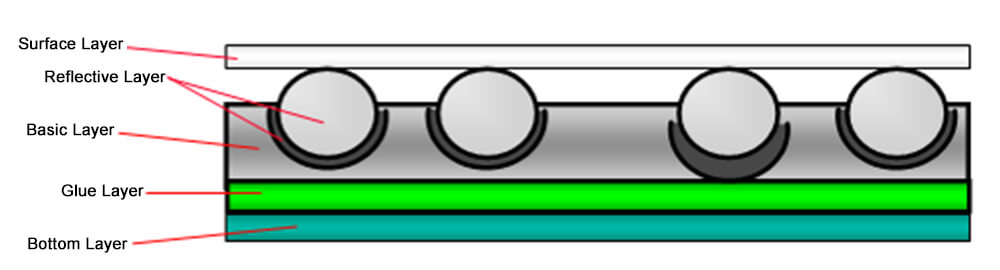
Figure 2: Initial Cross-Sectional Structure Layer Of Reflective Sheeting
Figure 2 is the basic structure diagram of the earliest glass bead reflective vinyl, from the diagram, can be seen that reflective sheeting is generally a film structure object composed of multiple layers of different substances such as surface layer (protective film), reflective layer (functional layer), grass-roots level (bearing layer), adhesive layer and bottom layer (protective layer), etc. The surface layer of the retroreflective sheeting generally consists of a resin film with good light transmission and weather resistance. The surface layer of reflective film is generally made of resin film with good light transmission and weather resistance, the reflective layer is composed of different materials according to different types of reflective films, such as tiny glass beads, micro-prism or metal reflective coating, the base layer is mostly a film made of resin organic compounds, the adhesive layer is generally epoxy resin glue, and the base layer is the protective layer made of thick paper.
Table 5 is the structure diagram of various reflective films, from which it can be seen that different types of reflective films, composition materials, and structures are also different.
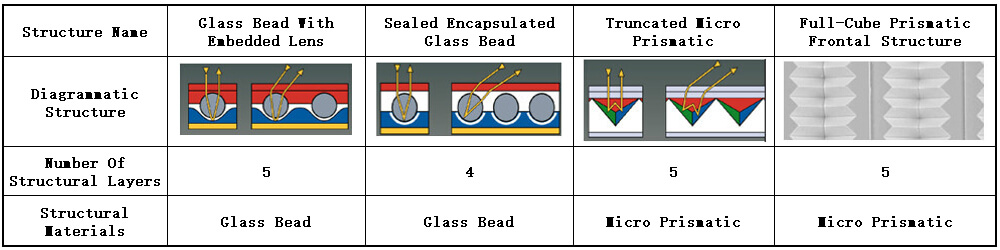
Table 5: Various Retroreflective Vinyl Main Structure Diagram Table
The primary role of reflective sheeting is to improve the surface properties of traffic signs so that they can be adapted to the needs of traffic in all-weather conditions and improve the safe operating conditions of the road.
Since there are differences in the reflective properties of different types of reflective films, when specifically applied to the production of traffic signs, there is a need for the corresponding specifications based on the function and purpose of the sign set. The science of studying such application specifications is seen as an important part of traffic control and safety technology by traffic safety engineering professionals around the world.
Traffic control and safety technology have been developed for hundreds of years. Since the first human traffic sign standard was introduced in 1908 in the United Kingdom, many countries around the world have continued to invest a lot of scientific research and technical resources to analyze and master the role and value of retro-reflective technology in the field of traffic safety. In this regard, the forefront is Europe and the United States, and other developed countries, their research results, in many ways, help China in a short period of more than 20 years, through the process from scratch to the best – China’s traffic sign reflective technology research started in the late 1980s, to traffic signs national standard GB5768 and GB18833, the national standard for reflective materials for traffic signs, are the main technical specifications.
4.1 Lens-Embedded (Conventional Engineering Grade) Retroreflective Sheeting
The lens embedded retroreflective sheeting, commonly called “engineering grade”, is the first kind of product of glass bead reflective vinyl, which is used to be called “engineering grade” series reflective film in the industry and was invented in 1937.
The traditional engineering-grade reflective film was introduced to China in the 1980s, and in the 1990s, a number of manufacturers began to emerge in China to manufacture this type of reflective film.
Since the 1940s, the material has been used successfully to make traffic signs. The introduction of this product, for the first time on roads, allowed drivers to travel at night to spot signs and reflective objects ahead of their route much earlier. With the advent of this material, the following problems that had been plaguing the road traffic safety management community at the time were solved, to varying degrees:
- 1. Road signs are not recognizable at night from a distance.
- 2. Active light sources are resource-intensive and some roads are not equipped to provide electric lighting.
- 3. Active light sources are likely to interfere with the driver’s vision and allow him to see things he does not need or should not even see.
- 4. A reflective sign that is capable of meeting the needs of low to moderate speed and narrow lane traffic (conventional speeds around the 1940s) in general.
To this day, such reflective films are still widely used in remote and rural roads in many countries, and in low-speed road environments where there is little interference from other light sources.
In the 1970s, there was a significant increase in the level of the industry, improved road construction technology, and increased vehicle speed, and in many places, engineering-grade materials could no longer meet the demand. In areas with small traffic flow, low speed of motor vehicles, no environmental interference light source, and many economically underdeveloped areas, especially on non-safety signs, engineer-grade reflective sheeting still has some applications.
After the advent of engineering-grade retroreflective film, it was once mainly used for making wayfinding signs, prohibition signs, warning signs, and directional signs as well as signs for general advertising. Along with the progress of retro-reflective technology and the continuous appearance of new materials, the brightness of engineering-grade reflective materials is gradually considered to be unable to meet the safety needs. In developed areas, they are no longer used for warning signs and prohibited signs. It is also difficult to find it on large fingerprint signs and high-grade roads. In the U.S. 2008 National Traffic Safety Standard, this type of reflective film (Class I sheeting in ASTM) is considered to have a minimum brightness that does not meet safety needs in many cases.
Engineer grade reflective vinyl backings, generally categorized as pressure-sensitive or thermal, can be completed with both types of adhesives. Various types of patterns can also be printed on them using screen printing techniques with the same type of ink. The backing plate for engineering grade reflective sheeting is an aluminum plate, and the construction operation temperature is generally required to be above 18 degrees Celsius. If the temperature is too low, the adhesive performance will be affected, resulting in the impairment of the significant life. Figure 3 is a diagram of the structure of the lens-embedded reflective film.
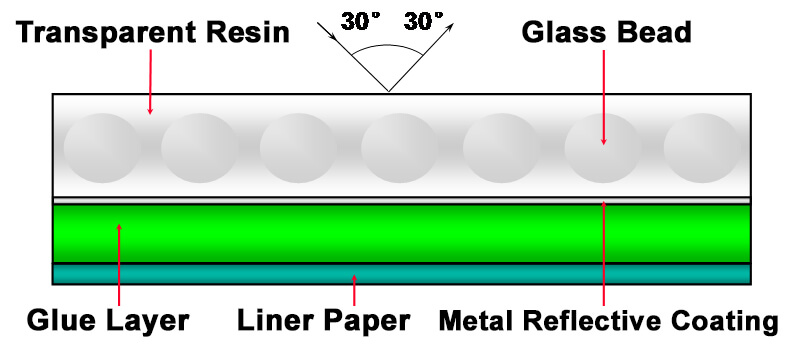
Fig. 3: Structural Diagram Of Lens-Embedded Retroreflective Film
The lifespan of engineer grade reflective film is generally 3 to 7 years, and the white film front two degrees (0.2º/-4 º) is generally around 100 cd/lx/m, depending on the manufacturer. Some manufacturers only provide reflective films for 7 years, after which the brightness retention value is at least 50% of the initial brightness value. Some manufacturers offer only 3 and 5 years of quality warranty. This is mainly due to the different weather resistance of the reflective film, the reflective film is made of the same raw materials, when used in different geographical climatic conditions, the length of life is different.
One more point to note is that the reflective brightness stability, reflectivity strength, and weather resistance of engineering grade reflective films are some of the important points to look into the quality of production of such reflective sheets. In these links, any shoddy work on any link can reduce the product cost, but its quality will be greatly discounted, especially the gap in weather resistance and reflectance parameters, which can clearly reflect the advantages and disadvantages of the engineering reflective film.
4.2 Lens-Sealed (High Intensity Grade) Retroreflective Sheeting
Lens-sealed reflective film is a durable glass-bead type reflective vinyl, customarily referred to in the industry as a “high-intensity” reflective film, developed in 1972.
Through qualified processes and materials, this high-intensity reflective vinyl is at least twice as reflective as engineering-grade reflective sheeting, and its internal vacuum support structure also solves the problem of condensation on the signage due to temperature changes, thus further improving the reflective ability of the material. When the material was introduced in the 1970s, it was successfully used to make traffic signs and saved a large number of lives, responding to the needs of technological advances at that time, when vehicle speeds increased and road conditions became better. Compared to engineering-grade reflective film, high- intensity reflective vinyl makes signs more visible even when they are at a greater angle and in brighter areas, effectively warning drivers of road hazards ahead.
The high-intensity reflective vinyl adopts glass bead reflective technology, which has incomparable reflective brightness and angle performance compared with the engineering-grade reflective film due to its innovation in product structure, but at the same time, it is also due to the structure of the high-intensity grade itself that leads to some insurmountable product defects, such as brittle and easy tearing, wrinkling, bubbles, surface honeycomb protrusion, high production energy consumption and large emissions. The limitations of glass bead technology have also hindered the improvement of high strength grades to higher brightness and better angularity.
High-intensity grade retroreflective sheeting is also material with adhesive backing and is generally classified as pressure-sensitive or heat-sensitive. Various types of patterns can be produced using screen printing techniques using the same type of ink.
The high-intensity grade reflective vinyl is generally composed of a resin film with good light transmission and weather resistance as the surface layer, a vacuum layer as the second layer, an embedded micro glass bead as the third layer, a metal reflective coating as the fourth layer, a resin bearing layer as the fifth layer, an adhesive as the sixth layer, and a backing paper protective layer as the seventh layer. FIG. 4 is a schematic diagram of the structure of the high strength grade reflective film and FIG. 5 is a typical appearance of the high strength grade reflective film.
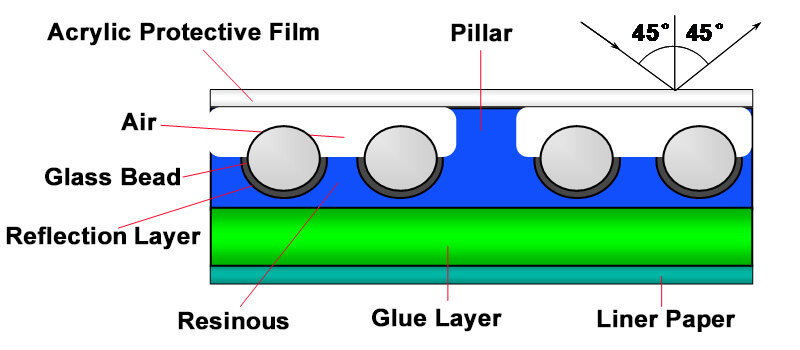
Fig. 4 Structure of high intensity grade reflective sheeting
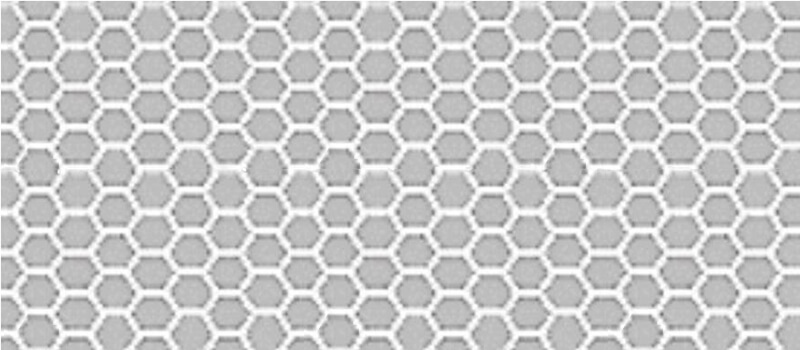
Fig. 5 Typical appearance of high-intensity grade reflective vinyl
High intensity reflective sheeting is mainly used to produce the main traffic signs such as road signs, prohibition signs, warning signs, and directional signs, etc. The introduction of high intensity reflective sheeting has shortened the time for drivers to recognize traffic signs and has significantly advanced the distance between the signs and obstacles ahead. After the advent of high-intensity reflective vinyl, the time for drivers to recognize traffic signs is shortened, and the distance between the signs and obstacles ahead is found to be significantly advanced, which greatly increases the time for taking safety precautions, reduces the occurrence rate of road traffic accidents at night and improves traffic safety. According to empirical research, the brightness of high-intensity grade retro-reflective materials, then engineering-grade retro-reflective materials, substantially increased. Since the 1990s, this high-intensity retro-reflective material has been widely used on China’s highways.
Since then, with the improvement of motor vehicle performance and road construction technology, huge changes in the urban environment, highways, and high-speed vehicles have increased substantially, the city light source is complicated, wide roads and sharp bends are endless, the driver’s foresight recognition of the visual distance, there are new requirements. Some of the shortcomings of high-intensity reflective materials, especially in the large-angle reflective properties and processing technology and cost, have been unable to compare with the emerging prism technology, and gradually began to be replaced.
In the second half of the 1990s, especially in the 21st century, the United States and Europe have started the process of replacing high-intensity grade materials with prismatic grade materials. Especially in 2004 the advent of the ” high intensity prismatic” retro-reflective materials, the use of prismatic technology, not only from the reflective properties, processing methods, energy-saving, and emission reduction, then the high-intensity level has been qualitatively improved, the price and cost, but also do not lose the high-intensity level materials, from now on, as the birthplace of the high-intensity level materials, the United States, has no longer produce this material, so that China has become the only producer of high-intensity grade reflective materials.
The lifespan of high-quality high-intensity reflective vinyl is generally 10 years, the brightness of the front side of the white film (0.2º/-4 º) is generally above 250 cd/lux/m2, under normal use conditions, the brightness retention value after 10 years is at least 80% of the initial brightness value, the substrate for the high-intensity retro-reflective sheeting is an aluminum plate, the operating temperature is usually required to be above 18 degrees Celsius.
4.3 Microprismatic Reflective Vinyl
The retro-reflective principle of micro-prismatic reflective vinyl is different from engineering-grade (lens buried type) and high-intensity grade (lens sealed type) reflective vinyl, engineering-grade and high-intensity grade reflective sheeting both adopt glass bead reflective principle, while the reflective principle of micro-prismatic reflective vinyl is to use the refraction and reflection of the micro-prismatic mirror. The main representative products of the micro-prismatic reflective film can be mainly divided into four categories from the retro-reflection characteristics and structure: truncated-angle prism that focuses on long-range recognition, a truncated-angle prism that focuses on near-range large-angle readability, a full prism that takes both long-range recognition performance and near-range readability into account, and new prismatic reflective film that combines these prismatic technologies with new material technologies. They are new reflective materials that have emerged in recent years in response to the diversification of application levels and in response to the needs of different levels.
4.3.1 Long Distance Prismatic Reflective Film
Long Distance Prismatic reflective sheeting is the first generation of micro-prismatic reflective film, came out in the early 1980s, referred to as LDP, the market can see the first generation of diamond grade, crystal grade, starlight grade, are such products. The frontal brightness of these reflective films is very high, the frontal brightness of white film (0.2º/ -4º) is generally above 800cd/lux/m2, and the distribution of retro-reflective light has no directionality, reflective film whether horizontal or vertical film, there is little difference in the reflective effect. However, under the large angle of incidence and observation angle, there will be a great attenuation of the reflective brightness. The microscopic structure of this type of reflective film is shown in Fig. 6. This kind of reflective film that highlights the frontal retroreflective luminosity is more suitable for contour markers, warning posts, etc., and not for traffic signs that require more apparent brightness at a reading distance. This early prismatic reflective film was a milestone in the design and development of the prismatic structure at that time, which had not yet been able to solve the problem of retro-reflective brightness at large viewing angles.
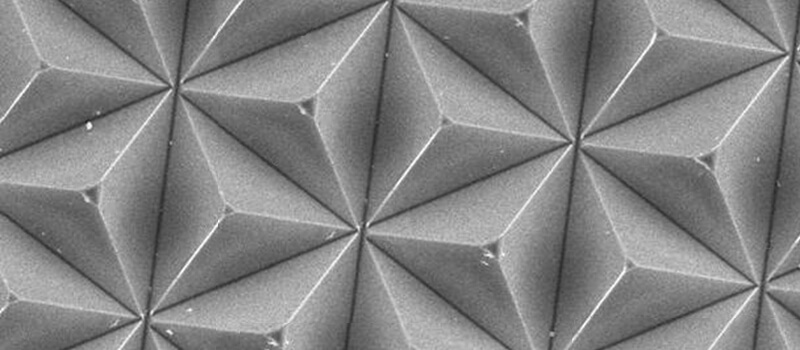
Figure 6 – Long Distance Prismatic Retro Reflective Sheeting Structure Diagram
4.3.2 Visual Impact Prismatic Reflective Sheeting
After the introduction of the first generation of micro prismatic reflective vinyl, a problem was found that when a motor vehicle actually drove into the reading distance of the sign, i.e., in the case of a large viewing angle, the brightness of the sign decayed so much that it was impossible to read the content of the sign within the reading distance, or it took longer to read it. From this, a large-angle truncated microprismatic structure has been used to create a Visual Impact Prismatic reflective sheeting to solve the problem of keeping the sign two degrees within the reading distance. Therefore, this VIP Reflective Sheeting, also described in terms of reflective properties, is a special type of prismatic reflective film.
Compared with the long-distance prismatic reflective sheeting, the frontal brightness of the Visual Impact Prismatic Reflective Vinyl is lower, but its reflective brightness will not have a great attenuation at the large incidence and observation angles. The large-angle corresponds to locations with multiple lanes and curves, as well as signs with complex content that require longer reading times, so this reflective film is suitable for traffic signs on urban roads and wide roads. Although its frontal reflective brightness at long distances is average (only relative to the long-distance prismatic grade, which can still be more than double the frontal brightness compared to the high-intensity grade), at close distances (distances where sign content reading is required), its reflective brightness is much higher than that of the long-distance prismatic reflective vinyl. Its directionality is stronger than that of the LDP reflective sheeting and can be adjusted to suit the need for reading according to the position and direction of the sign set. Figure 7 shows the structure of the VIP (Visual Impact Prismatic) prism under the microscope, which was introduced in the late 1980s and was once widely used but was discontinued after the advent of full-angle prismatic technology.
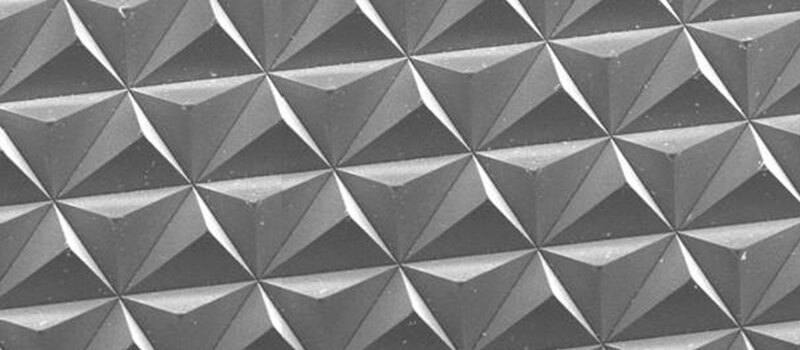
Figure 7: Structural Diagram of Visual Impact Prismatic
4.3.3 Full Cube High Intensity Prismatic Reflective Sheeting
It is a prismatic retro-reflective material completed by using a full cube prismatic structure. In short, it is a combination of prismatic structures that can realize full reflection by removing the part that cannot be reflected in the traditional micro-prism structure. It combines the two characteristics of long-distance and visual impact micro-prismatic reflective vinyl, which improves the reflective brightness at the large incidence and observation angles at distances of 50-250 meters while keeping the frontal brightness large and easy to find at long distances.
The advent of this full-cube high intensity prismatic reflective vinyl breaks through the academic barrier that prismatic reflective film can’t take into account both long-range and short-range reflective capability at the same time. According to the path and mode of vehicle light propagation, it finds the angle (incidence angle and observation angle) required for sign recognition in the ideal distance, and then determines the non-reflective areas on the traditional truncated micro-prismatic, and then removes these non-reflective areas, so as to realize 100% reflective structure area on the reflective sheeting per unit area, which is the so-called “total reflection”.
Of course, in terms of the actual reflective effect, this is only a theoretical reflective efficiency of 100%. In the actual production, due to the material and other conditions, reflecting the brightness of the lights 100% cannot yet be achieved, the best reflective efficiency is 58%, which is already much higher than other types of reflective vinyl, such as high-intensity level of reflective efficiency, only 23%. The best reflection efficiency is 58%, which is already much higher than other types of reflective films, such as the high-intensity level, which is only 23%. And from the observation angle of 0.2º up to 2º, w its retro-reflection efficiency can always be maintained at more than 50%. Fig. 8 is an electron micrograph of the full cube prismatic reflective film.
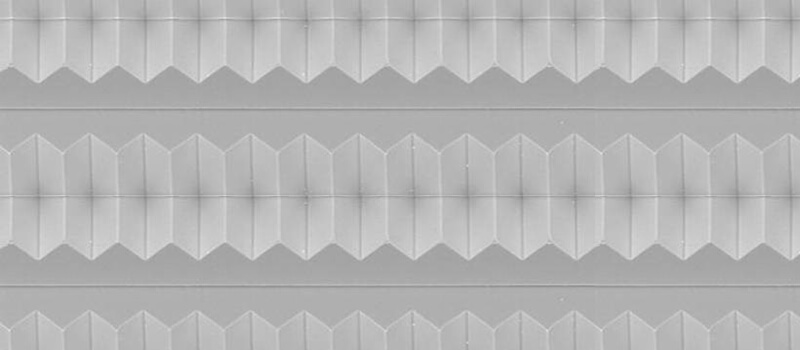
Fig. 8 Full Cube Prismatic Retro Reflective Sheeting Surface Structure Electron Micrographs
On the all-cube high intensity prismatic retroreflective sheeting, there are more than 930 units in one square centimeter of the material area to control the path of incoming and outgoing light after each microcrystalline cube is connected and arranged according to certain rules. The lower layer of the microcrystalline cube is sealed to form an air layer, which makes use of the light diffraction phenomenon to form an internal total reflection of the incident light so that the most superior reflective effect can be achieved without the use of a metal reflective layer. Compared with the traditional engineering grade and high intensity reflective sheeting, this HIP grade reflective sheeting is made of wear-resistant and high hardness polycarbonate material, and microcrystalline cube technology not only has its reflective performance doubled but also has its large-angle reflective performance greatly improved. The frontal brightness of this kind of holographic prismatic reflective film is more than six times that of engineer grade, and the frontal brightness of white film (0.2º/-4º) is generally over 600 cd/lux/m2, which is more than twice that of high-intensity grade, while the retro-reflection performance under large observation angle (0.5º and 2º) is about two to four times higher.
Full cube HIP reflective sheeting is a traffic marking material suitable for all classes of highways and urban roads. The application in Europe and the United States is beginning to gradually replace the investment and consumption of sign lighting. When making road signs, full-cube prismatic reflective vinyl can replace any grade of reflective vinyl if the long-term investment and safety benefits are considered. Under normal use conditions, after ten years of use, the full-cube prism reflective brightness retention value of the retroreflective sheeting is at least 80% of the initial brightness value, that is, after ten years, it can still greatly exceed the retro-reflective performance of brand-new high-intensity and engineering-grade reflective film, which is a more economical choice to examine from the point of view of scientific development. At the same time, if you use the same kind of ink, combined with screen printing technology, you can make all kinds of traffic signs with patterns.
Full cube high intensity prismatic reflective vinyl is mainly used in road signs, prohibition signs, warning signs and directional signs, etc., especially the signs that need longer time to read, signs with complex visual environment, as well as wide roads and high-grade highways, its performance is especially outstanding. The substrate for Diamond Grade reflective sheeting is aluminum, and the processing operation temperature is generally required to be above 18 degrees Celsius.
Figure 9 is a comparison of the retroreflective brightness values of engineer grade reflective film, high strength grade, truncated prism, and full cubic prismatic at various angles. With the advancement of science and technology, the photometric performance of full cube prismatic reflective sheeting at various angles has been significantly improved.
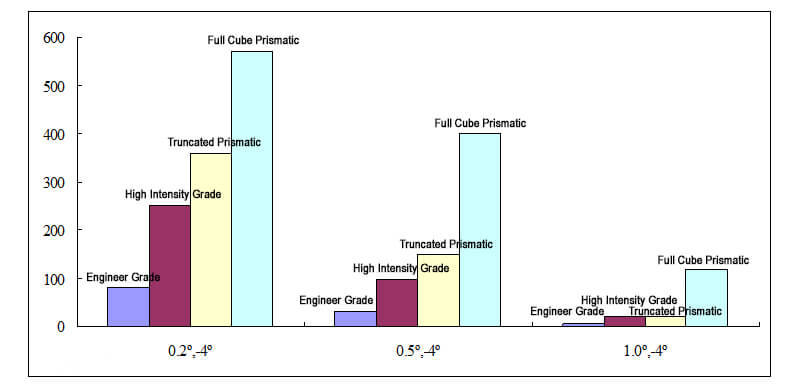
Fig. 9: Comparison of retro-reflection performance of various types of reflective film at different angles
4.3.4 Diversification of Prismatic Retro Reflective Vinyl Film
In recent years, prismatic reflective film, in the absence of major changes in structure, the focus of innovation has shifted more towards achieving richer light control effects and richer material properties through different material treatment technologies, in order to accomplish different retro-reflective capabilities, different flexibility, in order to adapt to the needs of different levels. In the market, reflective films commonly known as “super grade”, “High Intensity Grade” and prismatic engineering grade (new super engineering grade) are the new forms of prismatic reflective films. These reflective films have basically the same truncated-angle prism structure, but the material processing technology is different, forming different reflective effects, superior weather resistance, and processing adaptability in order to cope with different application needs.
Among them, especially the engineer grade prismatic reflective sheeting, due to respond to the needs of the market, came out at the beginning of the 21st century and quickly spread. The original design intention is to give full play to the advantages of the prismatic structure, to ensure that it can surpass all the functions of high-intensity reflective vinyl on the basis of high intensity grade reflective sheeting, but also in multi-angle conditions, with better retro-reflective performance, more superior cost performance.
These new prismatic reflective films have very high strength and thickness, eliminating the defects of reflective films such as easy tearing, wrinkling, bubbles, surface honeycomb protrusions, etc. in sign processing, greatly simplifying the difficulty of construction, making the sign processing process easier to control, and reducing the losses caused by poor processing. At the same time, due to the large surface brightness factor of reflective film, the retro-reflective properties are greatly improved. It not only has the superior retro-reflection coefficient in long-distance but also can still make the sign maintain better brightness under the general visual recognition requirement with the large observation angle in the close distance so that the driver can find the sign earlier and read the content of the sign more clearly in close distance. FIG. 10 is a schematic diagram of the structure of these prismatic structured reflective films. Through the material processing differences of the resin layer and cubic crystal surface, different reflective effects can be created.
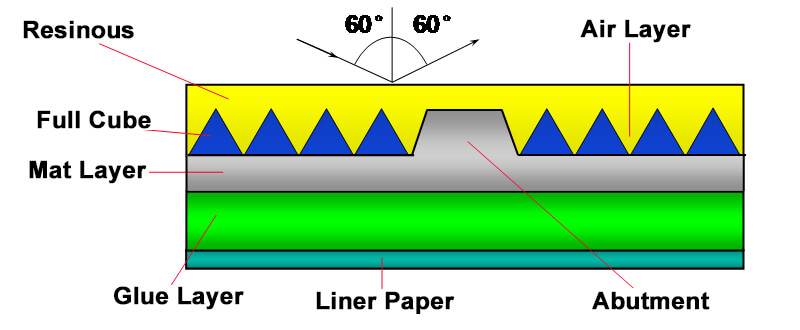
Fig. 10 Schematic diagram of the structure of the prismatic structure retro reflective film
The surface layer of these reflective films is mostly made of polycarbonate, which is not only more resistant to abrasion and scratching, but also can be matched with screen printing ink, and can be applied to thermal transfer printing to produce color traffic signs. At the same time, due to the improvement of the surface brightness factor, the signs are more eye-catching and vivid in the daytime, and also have better weather resistance.
EGP reflective sheeting, which was introduced in 2008, is also a brand new product concept. While guaranteeing the frontal brightness performance of the traditional engineering-grade reflective vinyl, it has made great progress in large-angle reflective performance, and its retro-reflective ability even surpasses the parameters of high-intensity reflective film; meanwhile, due to the use of polycarbonate material, this kind of reflective film possesses the ability of hard and high weather resistance, which can greatly improve the construction efficiency and provide more technical choice space for the application and promotion of retro-reflective materials!
4.3.5 Fluorescent Reflective Vinyl
After the full cube prismatic structure, the reflective film has not yet made any further breakthroughs in structure. However, there is still much room for development in the cost, material, and chemical coating of reflective films. Fluorescent reflective sheeting is a typical case in which the coating technology is improved to further optimize the reflective film function. Fluorescent full-cube prismatic reflective vinyl is a reflective film with a special optical effect by combining special fluorescent material with excellent weather resistance (general fluorescent material has poor weather resistance) and full-cube prismatic technology. There is a unique weather-resistant fluorescent factor in fluorescent reflective vinyl, which can absorb the visible light and part of the invisible light energy in the spectrum and increase the activity degree, thus converting the invisible light energy into visible light energy, making the reflective film’s chromaticity and luminosity play a more powerful role in the daytime, thus increasing the conspicuousness of the sign.
Since fluorescent reflective films are able to absorb the invisible energy within the spectrum and convert it, this allows them to have better color and luminosity, which is known as more vividness. This fluorescent reflective sheeting is much brighter and more noticeable in adverse weather conditions and when the sun’s rays are not as strong as they should be. The use of this fluorescent reflective vinyl in products for traffic safety devices is of great importance to ensure safe driving at dawn, dusk, or in inclement weather such as rain, snow, or fog. The application of fluorescent full cube prismatic reflective vinyl in foreign countries has been very common, such as fluorescent warning signs, fluorescent linear outline markings, fluorescent signs in road construction areas, etc. Full cube prismatic fluorescent yellow-green reflective vinyl has been approved by the U.S. Federal Highway Administration for pedestrians, non-motorized vehicles, and traffic signs in school zones; Full cube prismatic fluorescent orange reflective film is mostly used in construction zone signs. Countries around the world have also introduced corresponding standards, specifications, and technical conditions for fluorescent reflective films. Figure 11 is the comparison of fluorescent and non-fluorescent reflective vinyl.
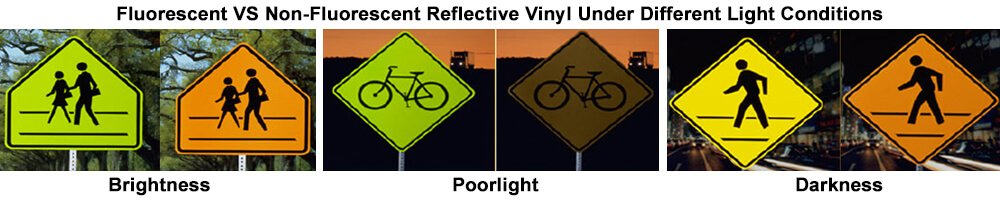
Fig. 11: Fluorescent VS Non-Fluorescent Reflective Vinyl Under Different Light Conditions
Under backlighting conditions, other traffic signs have poor color and luminosity, but the full cube prismatic fluorescent yellow-green reflective sheeting area, very striking. It should be noted that fluorescent reflective film is a combination of weather-resistant fluorescent factor and prismatic reflective film, the type of advertising material printed with lemon yellow, which is not part of this technology, does not have all the technical characteristics of fluorescent reflective vinyl, although the surface appears to be close to the color spectrum.
Chapter 5: Industrial Reflective Materials
Industrial reflective materials mainly refer to six levels of various reflective films, diamond grade reflective sheeting, High intensity prismatic grade reflective vinyl, high intensity grade reflective film, engineering grade reflective sheets, advertising grade reflective vinyl, and vehicle license plate grade reflective sheeting, and so on. It is mainly used for making various kinds of reflective signs, vehicle number plates, safety facilities, etc. In the daytime, its bright color plays an obvious warning role, and at night or in the case of insufficient light, its bright reflective effect can effectively enhance people’s recognition ability, see the target clearly, and arouse alertness, so as to avoid accidents, reduce casualties and economic losses, and become an indispensable safety guard for road traffic! And has obvious social benefits.
Chapter 6: How to Buy Reflective Sheeting
6.1 Confirmation of specifications
Before purchasing vinyl, make sure you know the specifications needed. Once you have determined the type of reflective sheeting needed, there is another critical choice to make. This is somewhat difficult because there is no consensus. Different manufacturers use different labels called “grades” to improve the quality of their reflective vinyl. 3M, ORACAL, Kiwalite offers commercial and engineer grade films. Avery offers “utility”, engineer, and super engineer grades. KWVINYL offers Engineer, Flexible Engineer, and Super Engineer grades. How do you choose the right product?
To simplify your choice, don’t pay too much attention to the “Grade” label on the film. Instead, look for outdoor durability ratings and flexibility. Since most films tell you what to expect, outdoor ratings are easy. Typically, the last three to seven years outdoors, although the newer Type II “Super Engineer” reflective films now last ten to twelve years.
6.2 Whether The Application Scene Is Flat Or Curved
This places consistency as a key factor. This is important because reflective vinyl is not made from the same PVC compound used in calendered and cast films. It’s made from a translucent acrylic resin designed to allow light to escape from a closed bead or prismatic. These masks can be brittle, and some films that are seven-year engineer grade products can only be used on flat surfaces. They are ideal for road signs, not for police and emergency vehicles. This usually causes problems when someone chooses a substandard reflective vinyl for a fleet application. The film will stick for a while and then begin to release from the curved surface. Having a newly applied graphic fall off the sheriff’s cruiser could be detrimental to your career. Therefore, make sure you check the specification.
6.3 Application Techniques and Digital Printing
Now that you know how to choose the right reflective product for your needs, we need to discuss application and printing. The most common mistake made when spraying reflective vinyl is using a spray solution. This is a big no-no. The adhesives used in these products do not stand up well when applied wet. Using any applicator, whether it is dishwashing liquid or RapidTac, can cause the vinyl to fail. Always wipe the reflective film dry.
The inclusion of reflective graphic elements in commercial vehicle wraps has made the reflective film much more attractive than it has traditionally been for municipal signs and emergency vehicles. This trend has sparked the imagination of many sign manufacturers, leading to many questions about whether or not it is possible to mark on reflective vinyl. The answer is yes.
If you are using an older thermal resin printer, you can print on the most reflective vinyl, although some of it may not hold the resin as well as others. If you use solvent or eco-solvent inkjet, you will be able to print on some reflective vinyl, but not all.
For best results, we recommend using our Commercial Grade Reflective Sheeting, a 640 mil Type 1 retro-reflective film designed for use on solvent and eco-solvent inkjet printers. Commercial grade Reflective Sheeting is a qualified seven-year film that meets ASTM D4956 and E-810 standards for visibility and reflectivity. To print on a PrismJET VJ48 or MUTOH ValueJet, use an ICC profile for glossy vinyl and set the platen and preheater to 40° and 45°, respectively, and set the drying temperature to 50°C.
There are also digitally printable reflective options from ORACAL, Kiwalite, and Avery. Oracal’s ORALITE 5650RA is a white reflective film with ORACAL’s Rapid Air exit liner, which helps with the bubble-free application of large vehicle graphics. As with most air exit films, it is more expensive. However, if you are installing large panels or signage, the air exit channel could be a lifesaver.
6.3 Custom printing
If you already have a complete design and need custom printing, we suggest you come to us directly for customization, our factory has professional technicians who can customize your product with longer life, better reflective effect, more economical, as well as more in line with your expected results.
For example, if your custom reflective stickers need to be constantly connected with corrosive solutions, or car wash fluid, etc., we would recommend that after printing the reflective sheet, we cover the stickers with a layer of acrylic film to insulate the printed pattern from contact with corrosive solutions, which can ensure that the stickers will last up to 10 years without fading.
Chapter 7: Conclusion
As your business grows, you will have the opportunity to sell and install municipal signage or fleet markings for local police departments and emergency vehicles. Be prepared for these important customers. Make sure you get the specifications. Then select the correct type and grade of reflective sheeting, especially if you plan to print the job. Follow the manufacturer’s instructions to dry and properly apply them to the surface. Professionally installed municipal signage will help your community thrive and reflect positively on your business.
KWVINYL is looking forward to wholesale reflective material distributor cooperation, if you are, please don’t hesitate to contact us for more details.
What is The Difference Between Reflective and Retro Reflective?
The tape on heavy vehicles is often called reflective tape, such as DOT C2 Reflective Tape, ECE 104 Reflective Tape, SOLAS Reflective Tape, etc., but is actually retro reflective tape. There is a big difference between reflective and retro reflective. Reflective is like a mirror that reflects light, it reflects the light in a different direction (the angle between the angle of reflection and the normal is equal to the angle between the angle of incidence and the normal), as in Figure a. Retroreflection is the reflection of light back the way it was intended, parallel to the incident light, as in Figure b.
Retroreflective materials are made of thousands of tiny glass beads or micro prismatic that reflect light and send the focused image directly back to the original light source. Headlights on a vehicle, for example, allow the driver to not only see an illuminated object in front of them but also to identify what that illuminated object is – a sign or a pedestrian.
What is Reflective Sheeting and How Does It Work?
Reflective sheeting is also called retroreflective sheeting is self-adhesive retroreflective material, which is primarily used for road safety, vehicle registration plate, commercial signages, construction traffic warning signage, traffic signages, this is to increase the nighttime visibility with the headlamps. This reflective sheeting also can apply to a scanning range of barcodes in the factory warehouse. Reflective sheeting is a kind of security film for the vehicle number plates, can be embossed and hot stamping onto aluminum, the watermarks are always embedded into the reflective sheeting by KWVINYL, this is for the security purpose not to fraud the number plate. The principle of retroreflection is reflecting light back towards its source, the simplest retroreflector is a glass sphere or bead, when a light beam, such as a car headlight is directed at it, the majority of the light bounces off, but a certain amount of light will pass through the front surface, and it bent or refracted roughly towards the center of the rear surface. Some light hits the rear surface of the beads, refracted back to the original source.
Glass Bead Reflective Vinyl & Prismatic Reflective Sheeting
There are two technologies for reflective sign sheeting materials, glass bead reflective vinyl and micro prismatic reflective sheeting. The prismatic type is also a full-cube corner reflector. Glass bead reflective sheeting performs well at wide angles, while prismatic reflective sheeting is brighter.
What is Diamond grade reflective sheeting?
Diamond grade reflective sheeting is a prismatic reflective vinyl with full cube construction, it will return 80% of the light back to the original lights, such as drivers on the road. Nowadays, cars getting more and more, the highway becomes much wider than before, to install diamond grade reflective vinyl, the reasons are speed is fast on the highway, and the road is wide.
What is HIP Reflective Sheeting?
HIP reflective sheeting is micro prismatic type, meets ASTM D4956 Type IV, this reflective vinyl is widely applied for traffic and road signs, barricades, vertical delineators.
How To Choose Reflective Sheeting By Application?
PVC surface reflective film for digital printing Acrylic/ PC surface reflective film suitable for screen printing PET-faced reflective vinyl is the most economical and suitable for lettering machine cutting. All face reflective sheeting are available for UV printing. All reflective sheets can be made into reflective tape according to your requirements.
How to use reflective sheeting
Choose A Suitable Substrate Material
It is recommended that it be applied to clean and flat aluminum or stainless steel plates, after proper treatment. It is not recommended to apply it directly on the surface of plastic, rubber, wood, or other materials. Of course, if you are required to apply the reflective tape to other non-aluminum or non-stainless steel sheets, please take measures according to the adaptability of the reflective film before applying it.
Treatment of the substrate
Freshly delivered aluminum and stainless steel plates have very smooth surfaces that are not conducive to adhesion. Need to use 400-500 sandpaper to grind and paste in the direction of a circular arc. Body reflective signs should be pasted on the surface of the body that is unobstructed, easy to see, flat and continuous, free of dust, water, oil, rust, and paint deformation.
The Substrate Should Be Cleaned Before Laminating
Before pasting, the dust of the surface to be pasted should be wiped off first. For the parts that have oil stains and stains, they should be removed with a soft cloth dipped in degreasing solvent or cleaning agent, and washed with water, and finally dried. For the parts whose paint surface has been softened, rusted, and deformed, the paint surface should be removed, polished with sandpaper, and do rust-proof treatment, and finally paste the reflective sign of the vehicle body. When Can’t Paste Directly When the surface of the car body cannot be directly pasted reflective signs, the reflective signs of the body should be pasted on the strip liner which has certain rigidity, strength, and anti-aging. The strip liner is then firmly pasted or riveted to the body of the vehicle. Do not affect the performance of the reflective sheeting It is reported that in the pasting method, the body reflective signs shall not be drilled or slotted after pasting, otherwise it will affect the performance of vehicle lighting and signaling equipment.
What Is Reflective Sign Sheeting?
Reflective sheeting rolls are available in different levels of reflective value, which come in commercial-grade, engineer grade (EG) vinyl, high-intensity grade sheeting, high intensity prismatic (HIP) retroreflective sheeting, and diamond grade (DG) reflective vinyl. To apply for different grades of retroreflective vinyl, depending on the road traffic in your country. For example, if you are making traffic signages for the highway, it is better to choose the high-intensity prismatic grade or diamond grade reflective sheeting. If you are making traffic signage for city road, countryside road signage, engineer grade reflective sheeting is your best choice.
Do You Produce Reflective Sheeting For Windows?
The reflective sheeting for windows has two types, one is to reflect the sunlight, we do not produce this type of reflective film. another type is called second number plate, which is widely used in Mexico and the USA, we do manufacturing this type of reflective sheeting. The unique is the adhesive is in front of the reflective film and sticks onto the car window.
Do You Produce Reflective Sheeting For Greenhouse
This is NOT the product we produced, our reflective sheeting is for road traffic, car license plate, commercial sign, and vertical barrels.
What Are The Best Hi Vis Colors?
Fluorescent color always the best choice to be high visibility in the daytime or poor lights, add on reflective fabric tape, it will enhance visibility at night time. Fluorescent yellow reflective sheeting use for warning signs, and can be cut to fluorescent yellow reflective tape, use for school car, make them high visibility at poor lights.